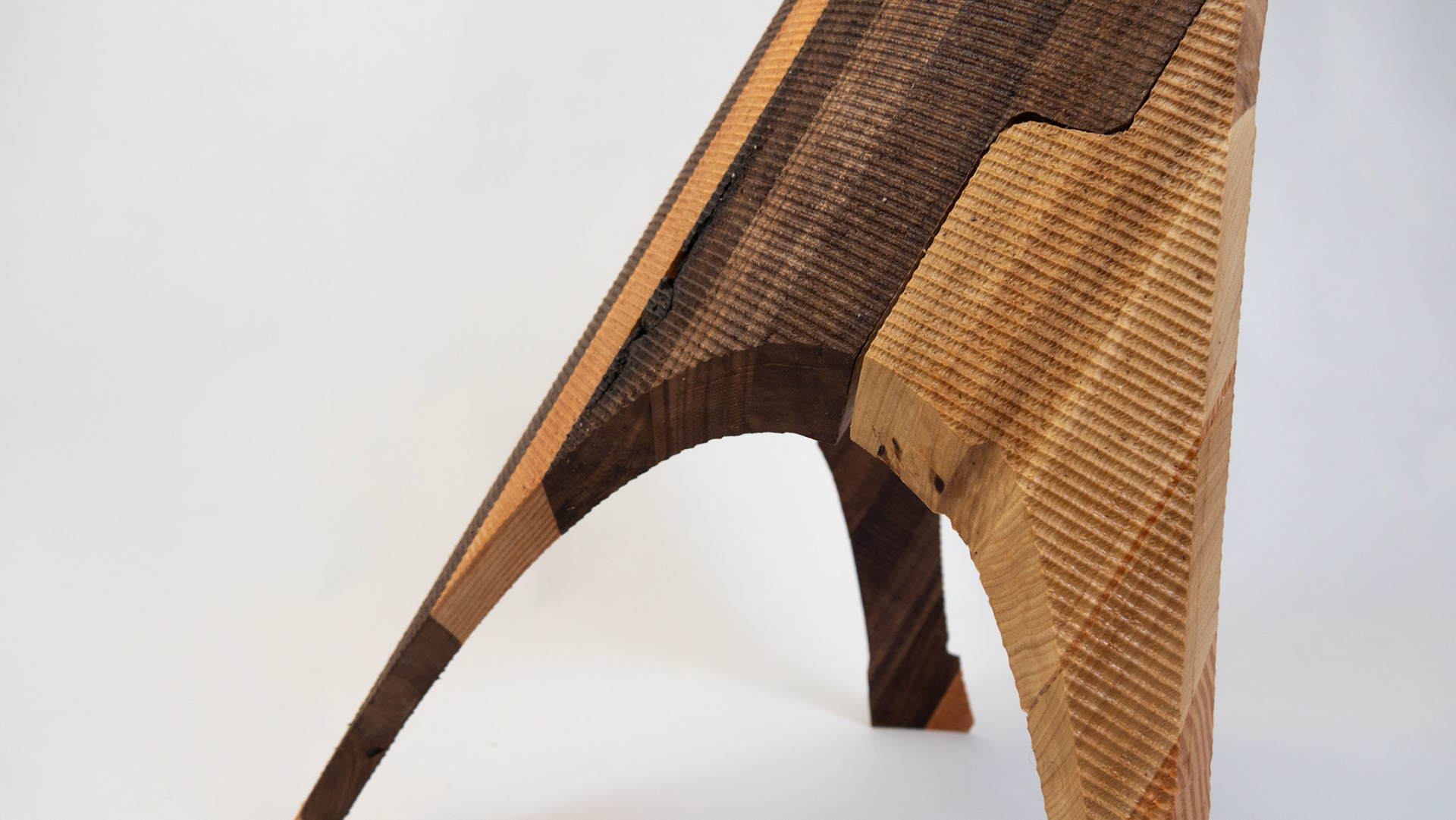
Functionally Graded Timber Structures
The Inner Forms: Functionally Graded Timber Structures project explores the intersection of robotic fabrication, computational design, and machine learning to develop a more material-efficient approach to timber construction. This research tackles the challenge of reducing wood waste by optimizing how timber is processed, laminated, and milled using a barrel construction strategy and 7-axis robotic non-planar milling.
Through this workflow, timber components are strategically placed to balance structural strength and flexibility, integrating hardwood in high-stress areas and softwood where flexibility is beneficial. Additionally, the project introduces machine learning-driven fabrication, utilizing both a YOLO-based wood detection model and a sound classification system to autonomously adjust robotic milling speeds based on wood species.
The research is structured into four key areas:
Form Finding – Using interpenetrating cylindrical geometries to optimize structural behavior.
Wood Lamination – Exploring hybrid material layering and cellular automata-driven toolpath generation to reveal distinct material aesthetics.
Robotic Fabrication – Implementing non-planar milling techniques and precision joinery to enhance efficiency.
Machine Learning – Creating an adaptive, autonomous milling system that optimizes the fabrication process in real-time.
This project demonstrates how computational design, robotic fabrication, and AI-driven automation can redefine timber construction, improving material efficiency, scalability, and structural performance while significantly reducing waste.
Institution: University of Pennsylvania
Lab: Advanced Research and Innovation lab
Instructor: Alicia Nahmad Vazquez, Patrick Danahy
Co-Instructors: Mahsa Masalegoo
Lab Managers: Nicholas Sideropoulos, Shunta Moriuchi
In Collaboration with: Zitong Ren, Burcu Gocen, Qingyang Xu.
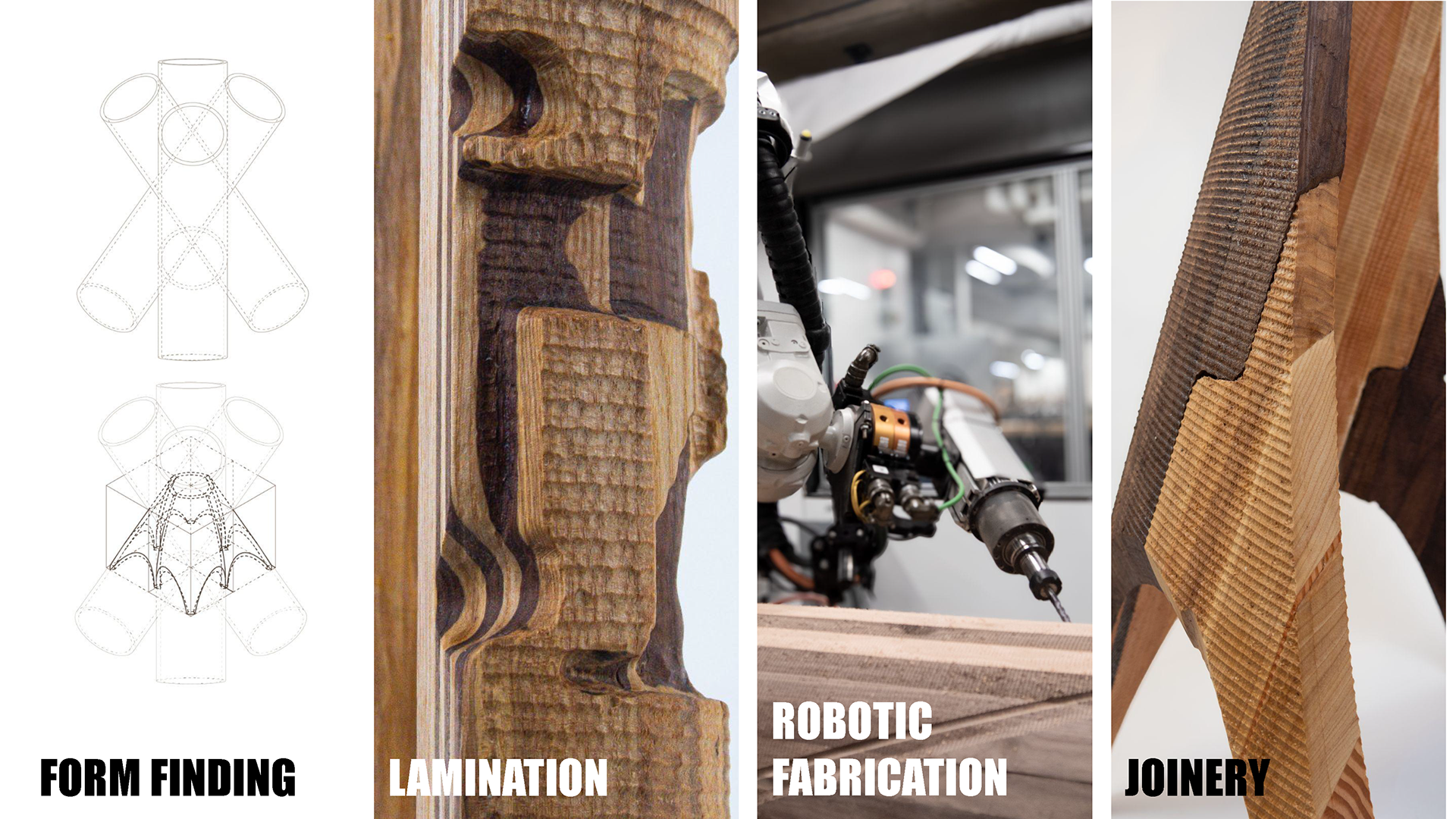
[01] form Finding:
Inspired by Frei Otto’s shell structures, this project employs interpenetrating cylindrical geometries to generate self-supporting timber shells. Through a computational form-finding process, these interwoven cylinders define a structurally efficient system that optimizes material distribution while allowing for geometric flexibility. This method enables the creation of complex yet buildable forms, balancing aesthetic exploration with structural performance. By leveraging computational tools, the form-finding process ensures that each shell maintains stability and efficiency, reducing material waste while maximizing aesthetics potential.
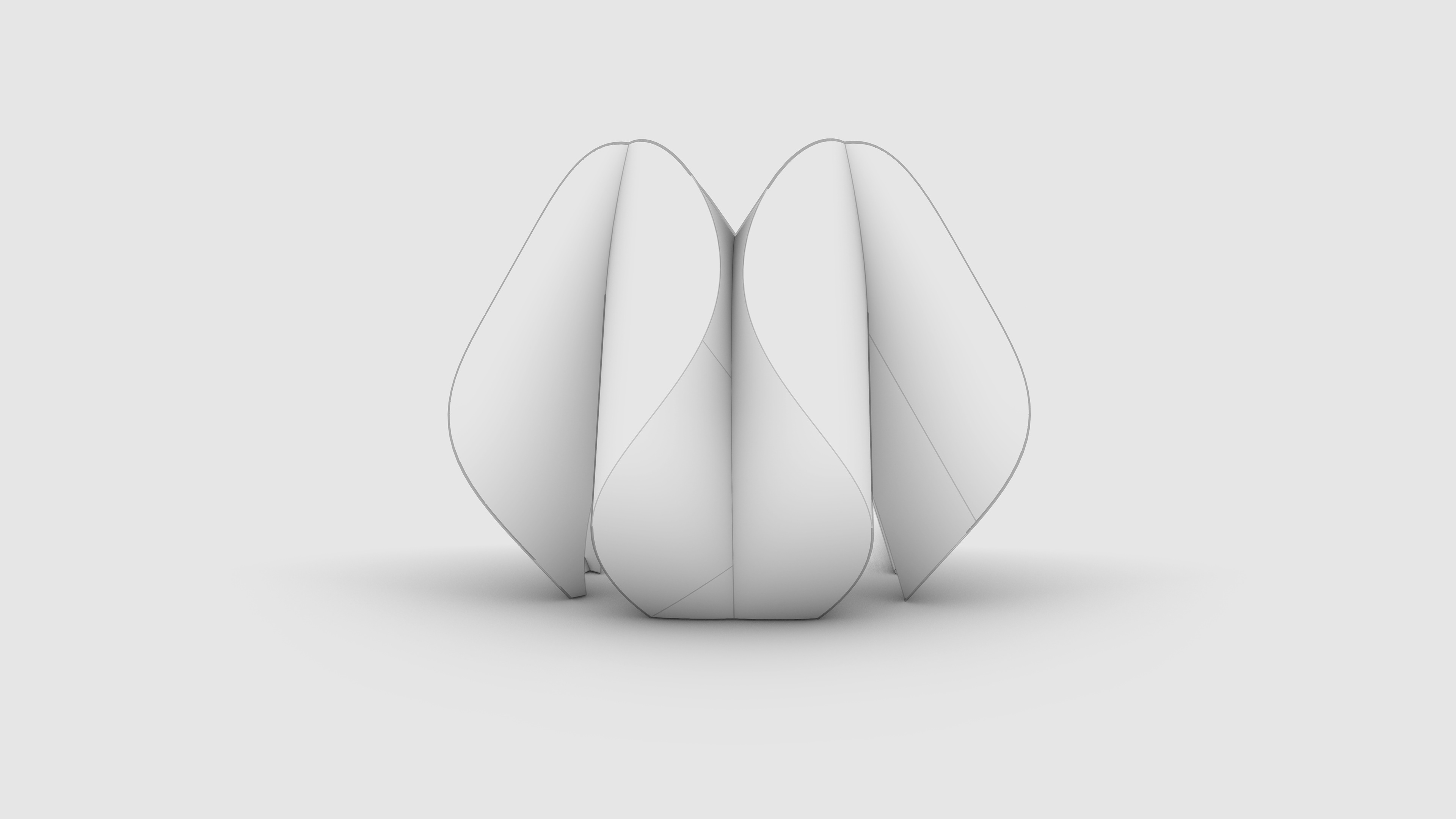
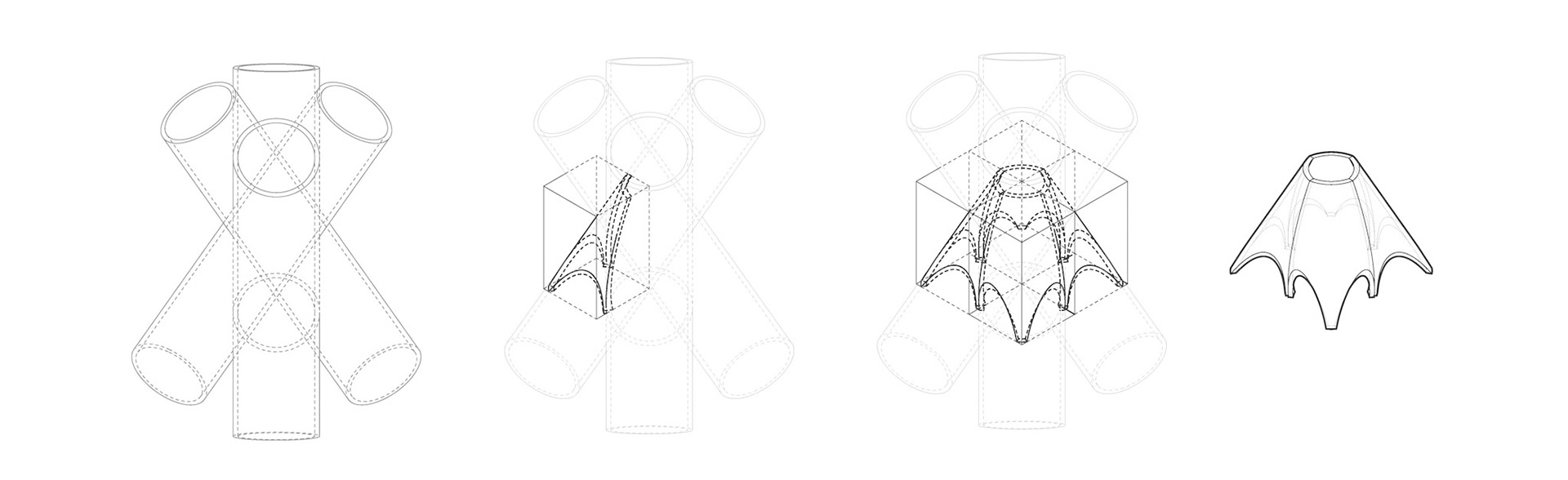
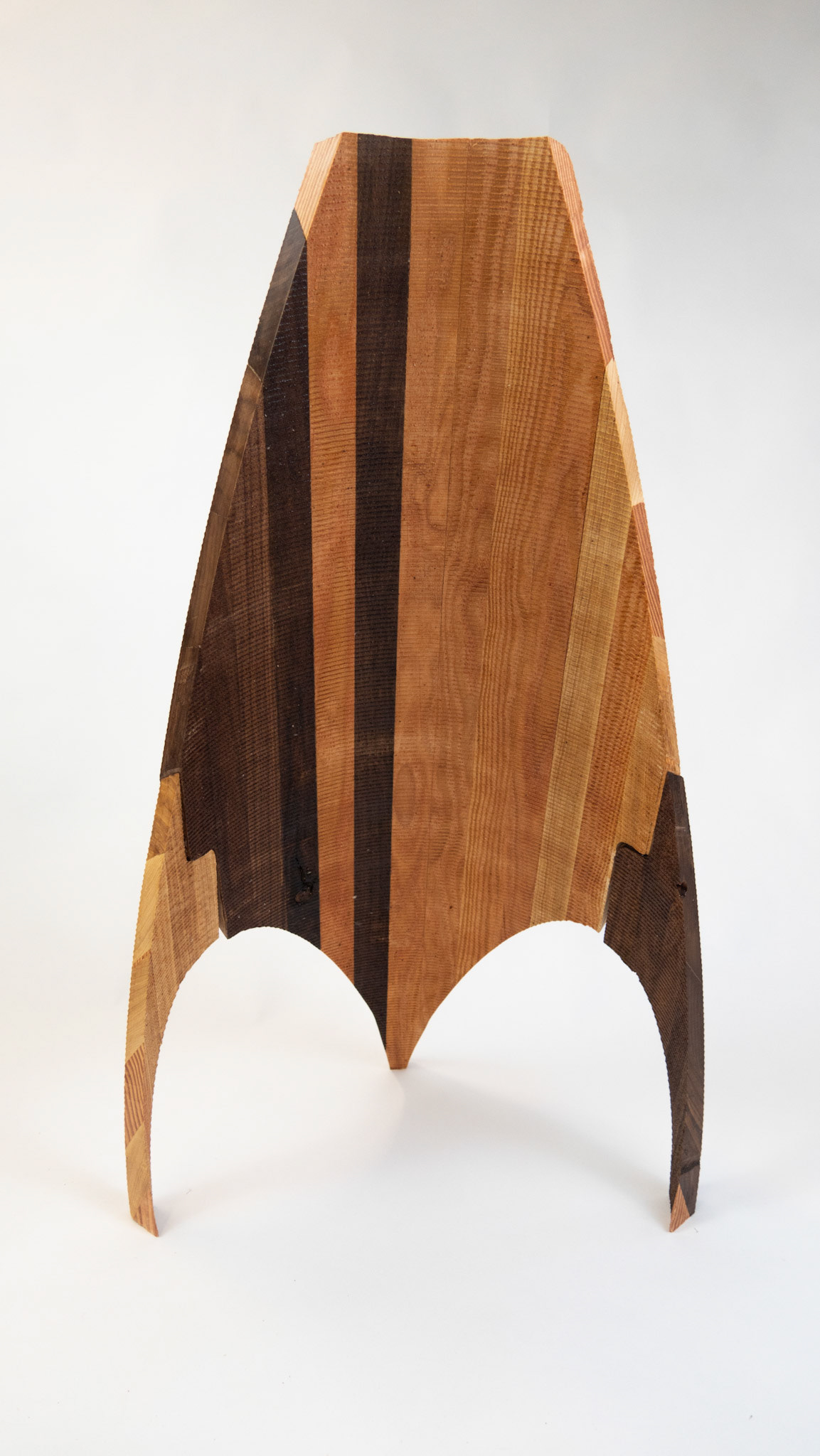
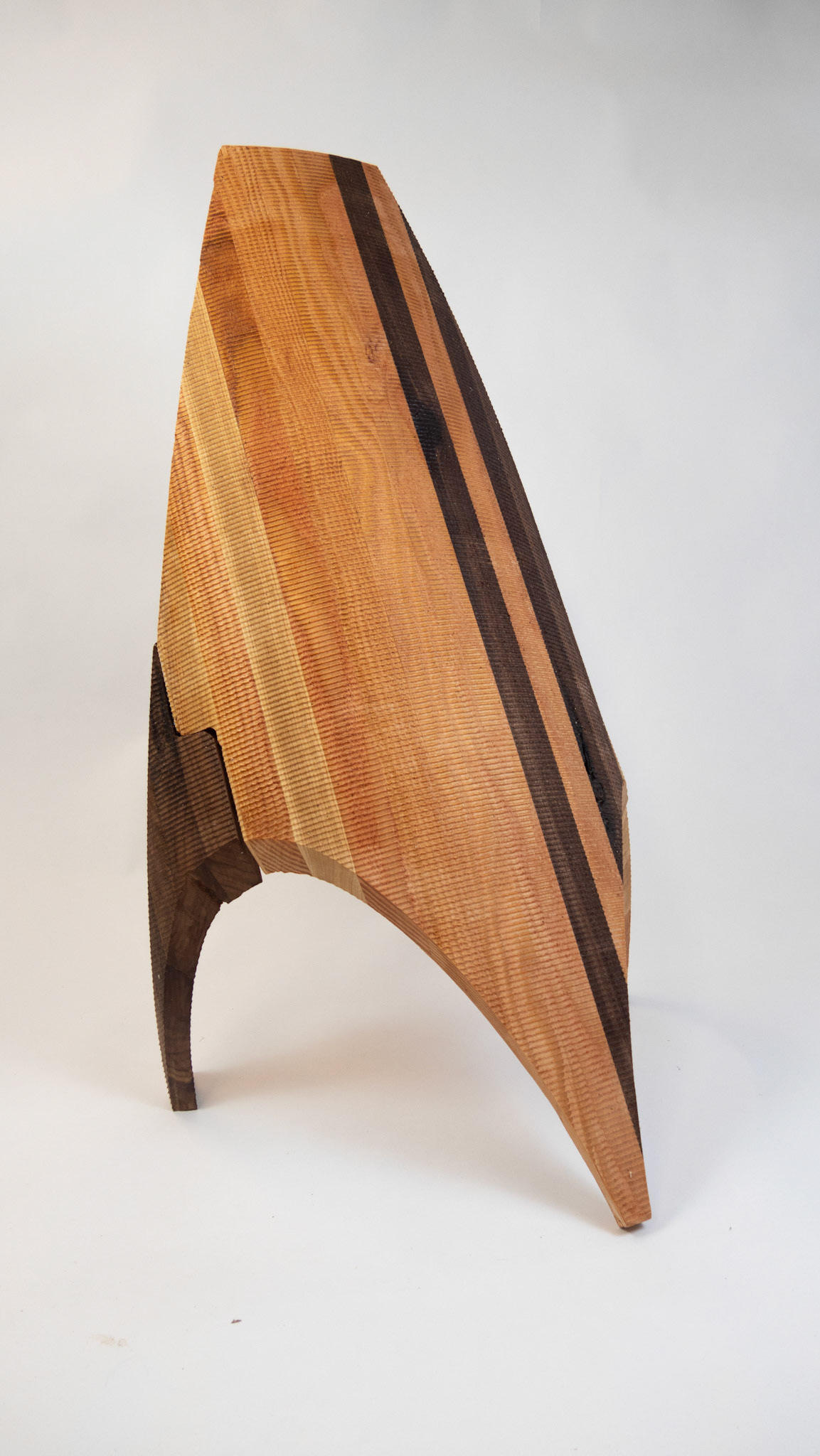
[02] wood lamination:
This research explores double lamination as a method to generate unique material-driven aesthetics. By layering thin sheets of different wood species, the project creates functionally graded timber surfaces, where material properties and visual patterns emerge through computational fabrication.
A custom cellular automata algorithm was developed to generate dynamic toolpaths for robotic milling. Each time the model runs, the algorithm produces a new, unique pattern, ensuring that no two pieces are identical. The robot then mills along these computationally derived paths, selectively revealing different layers of wood to create intricate grain patterns.
This study was driven by an interest in understanding the limitations and possibilities of robotic milling when applied to laminated timber. Instead of imposing predetermined aesthetics, the approach allows the process itself to define the final outcome—introducing an entirely new design language that is inherently tied to material performance and digital fabrication constraints.
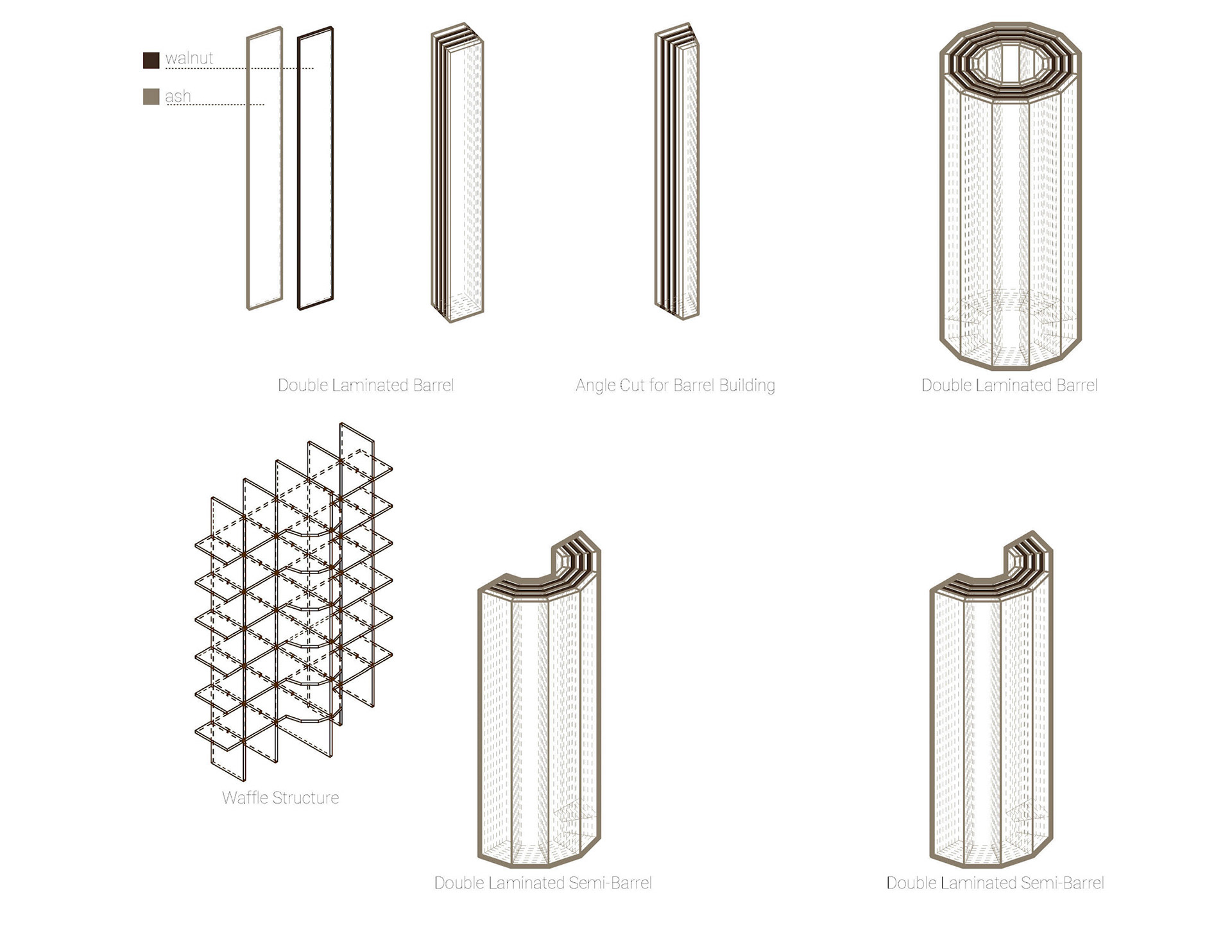
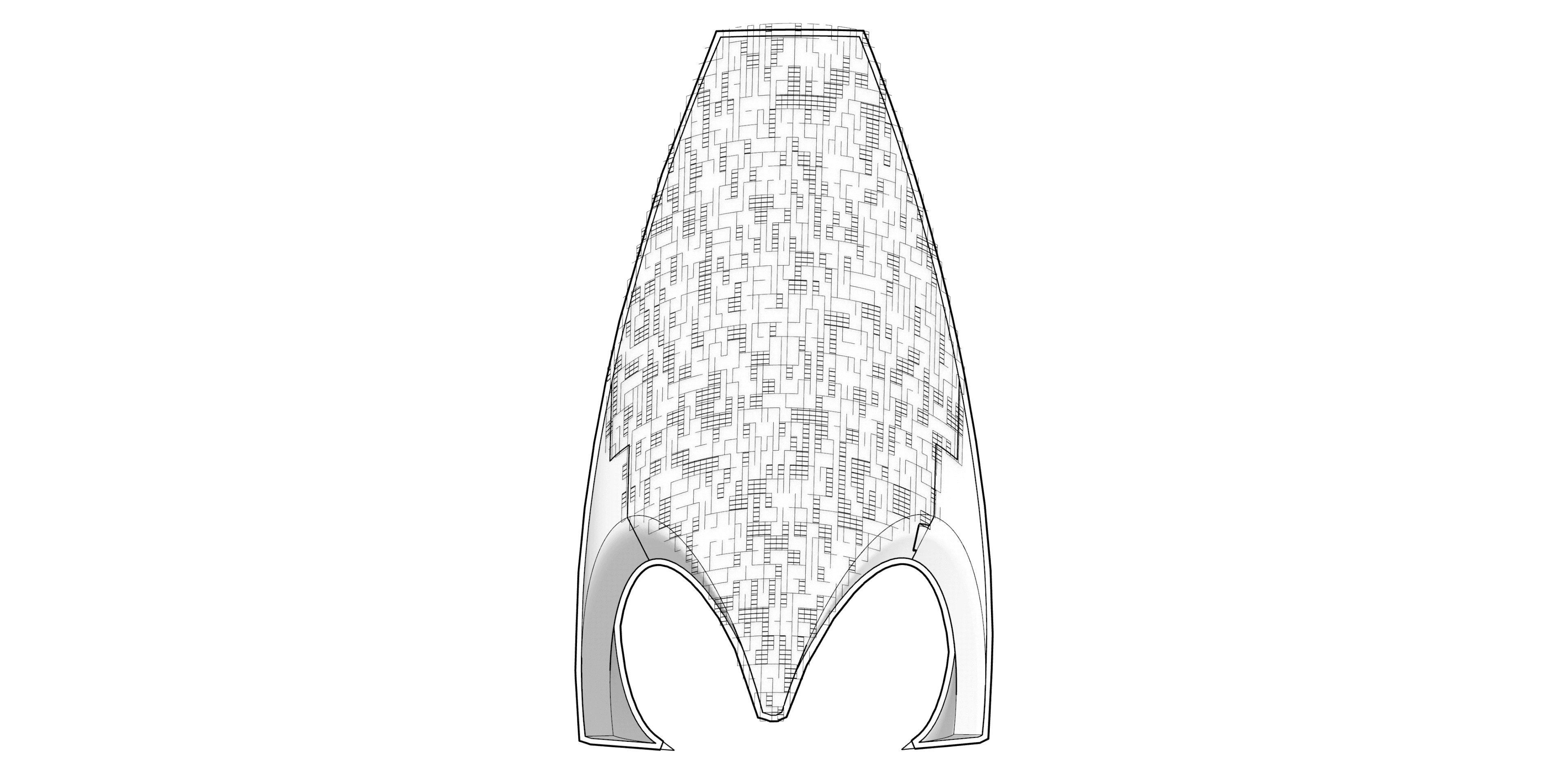
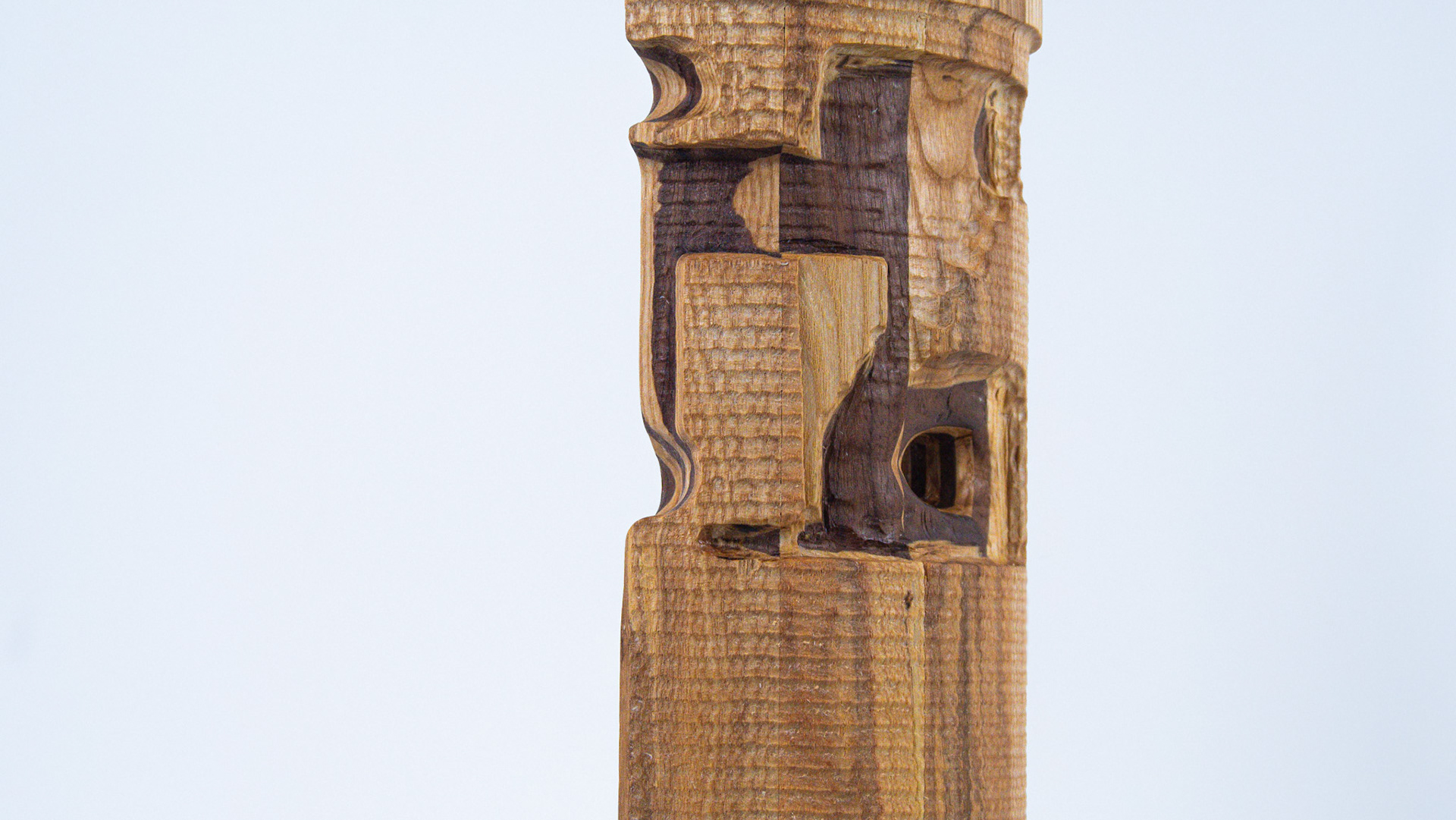
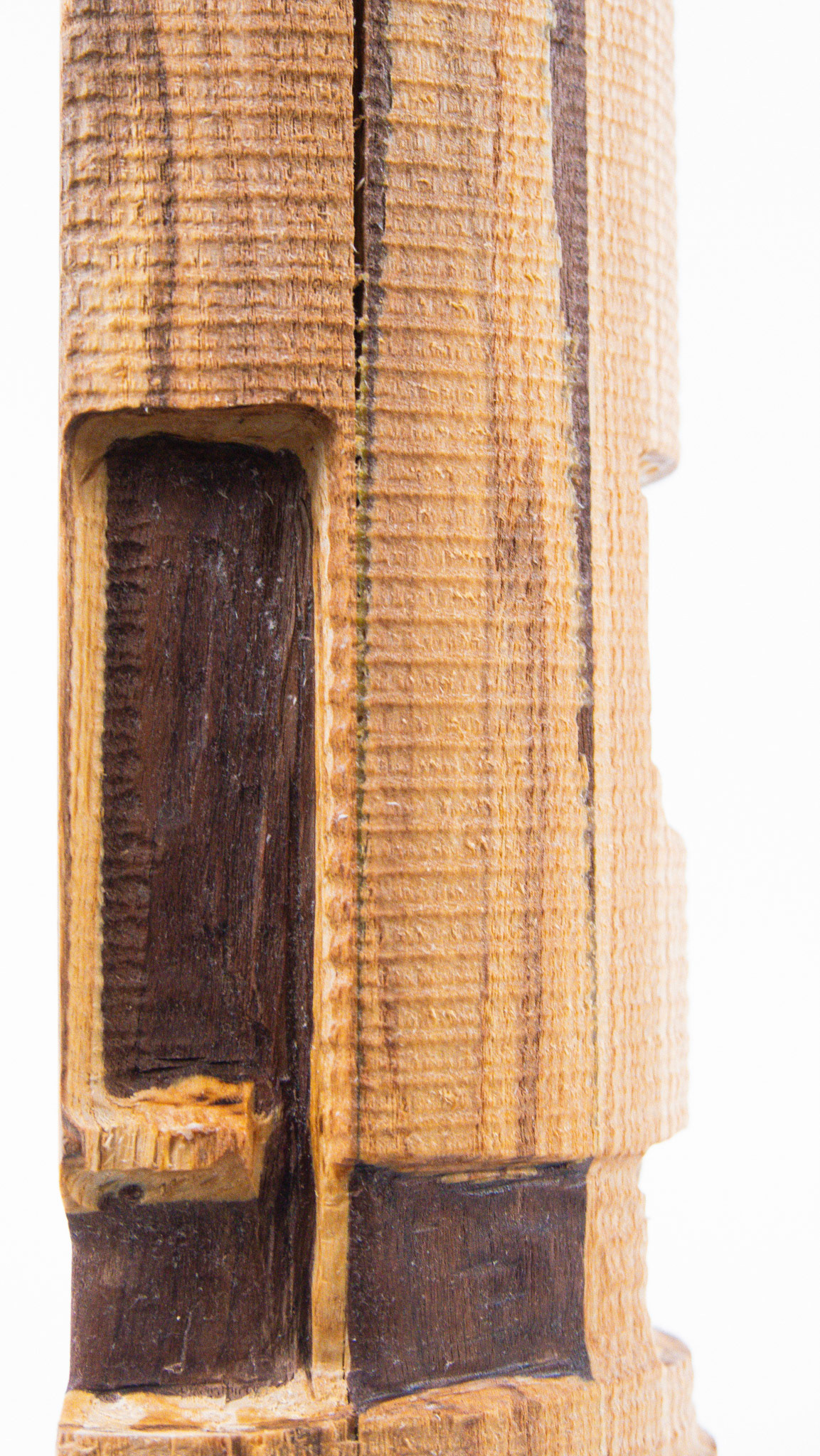
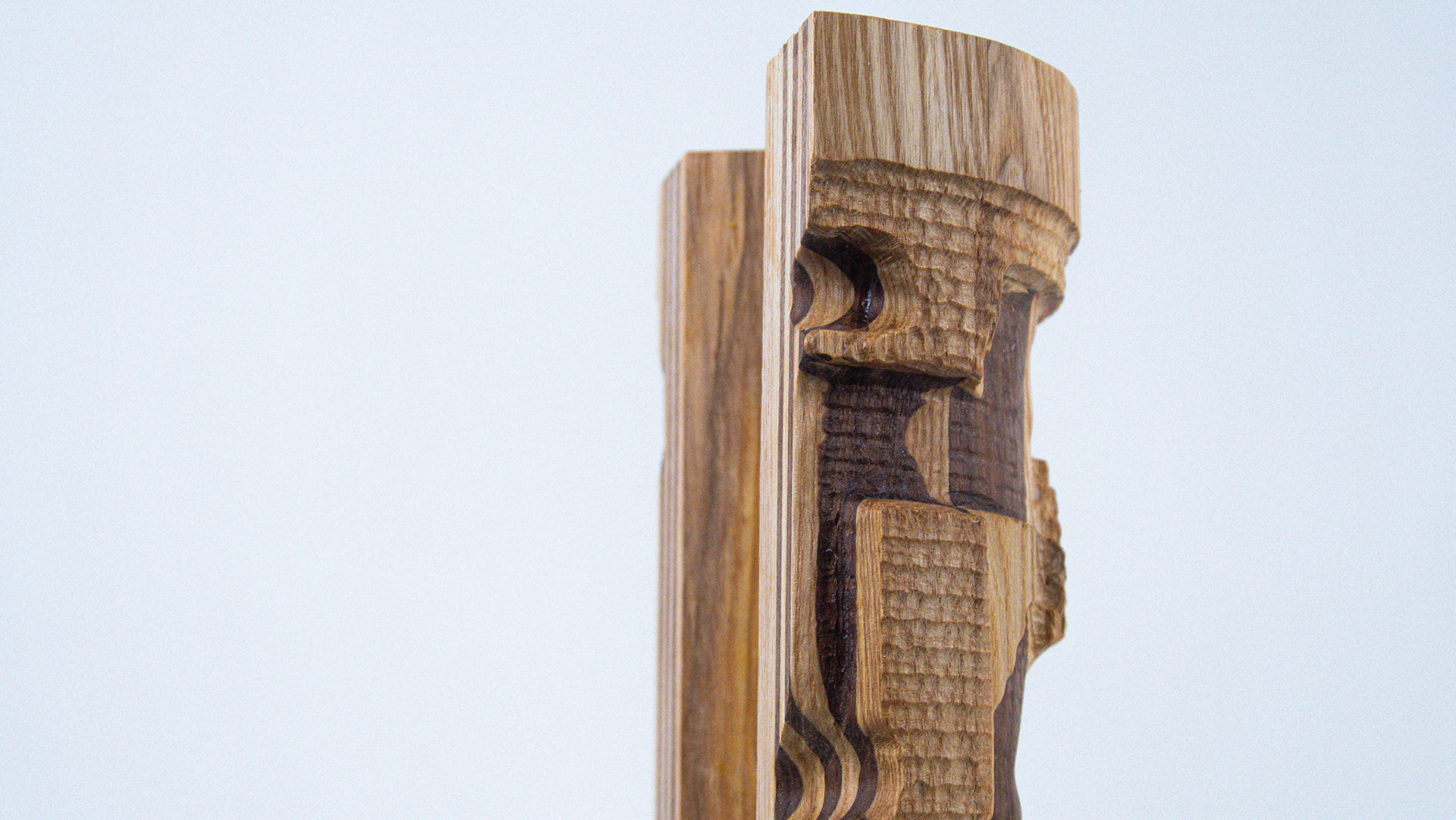
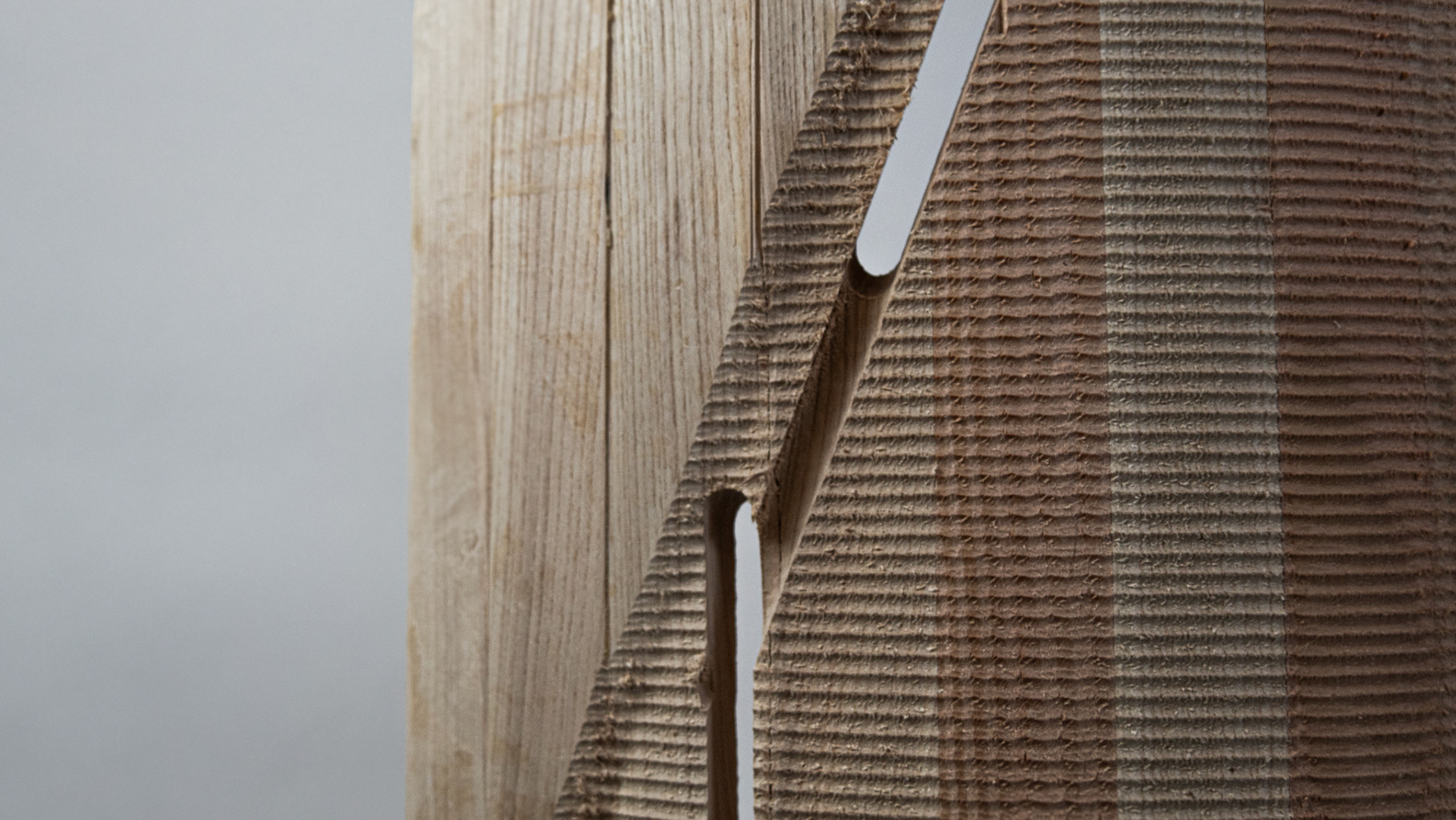
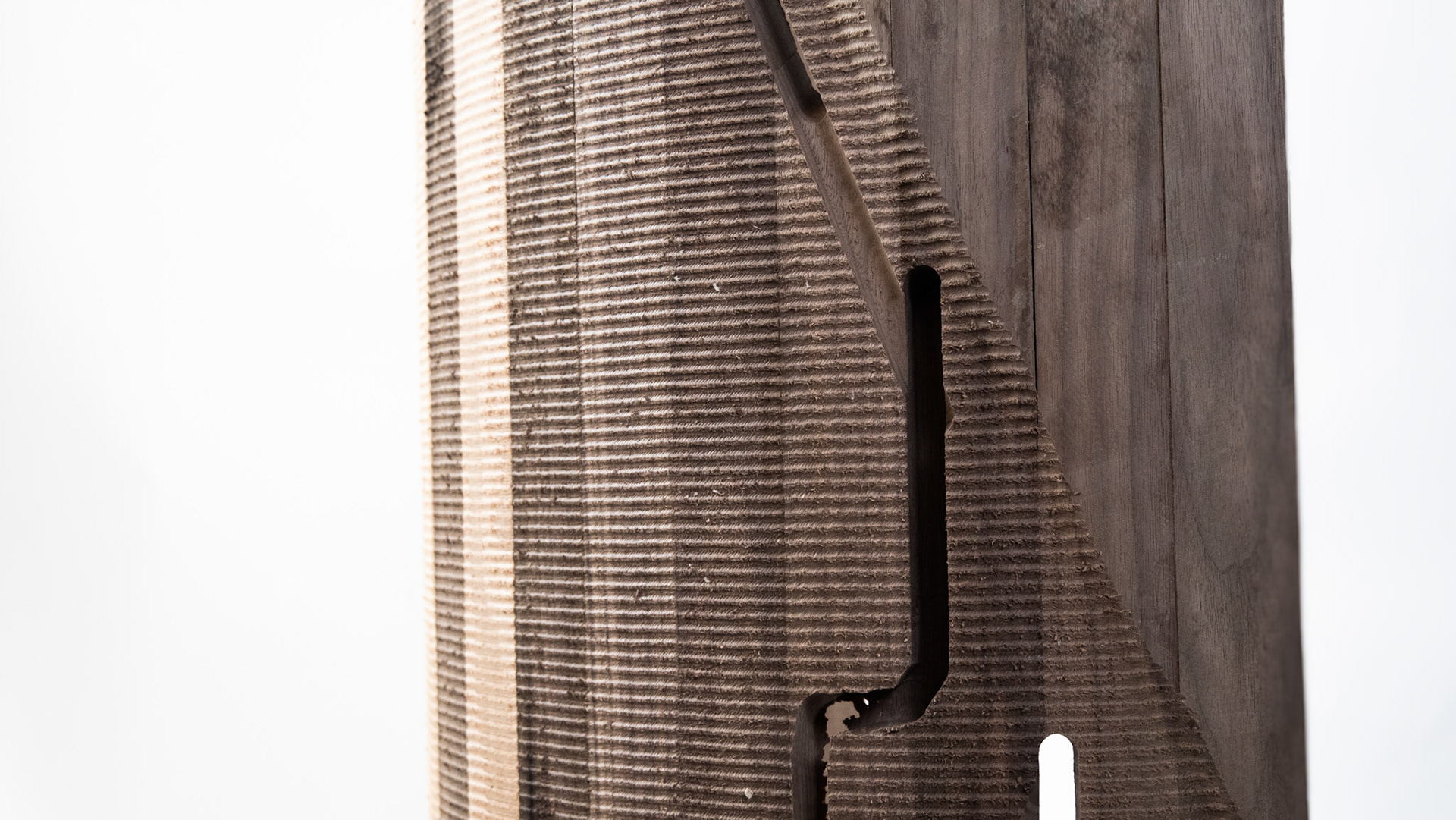
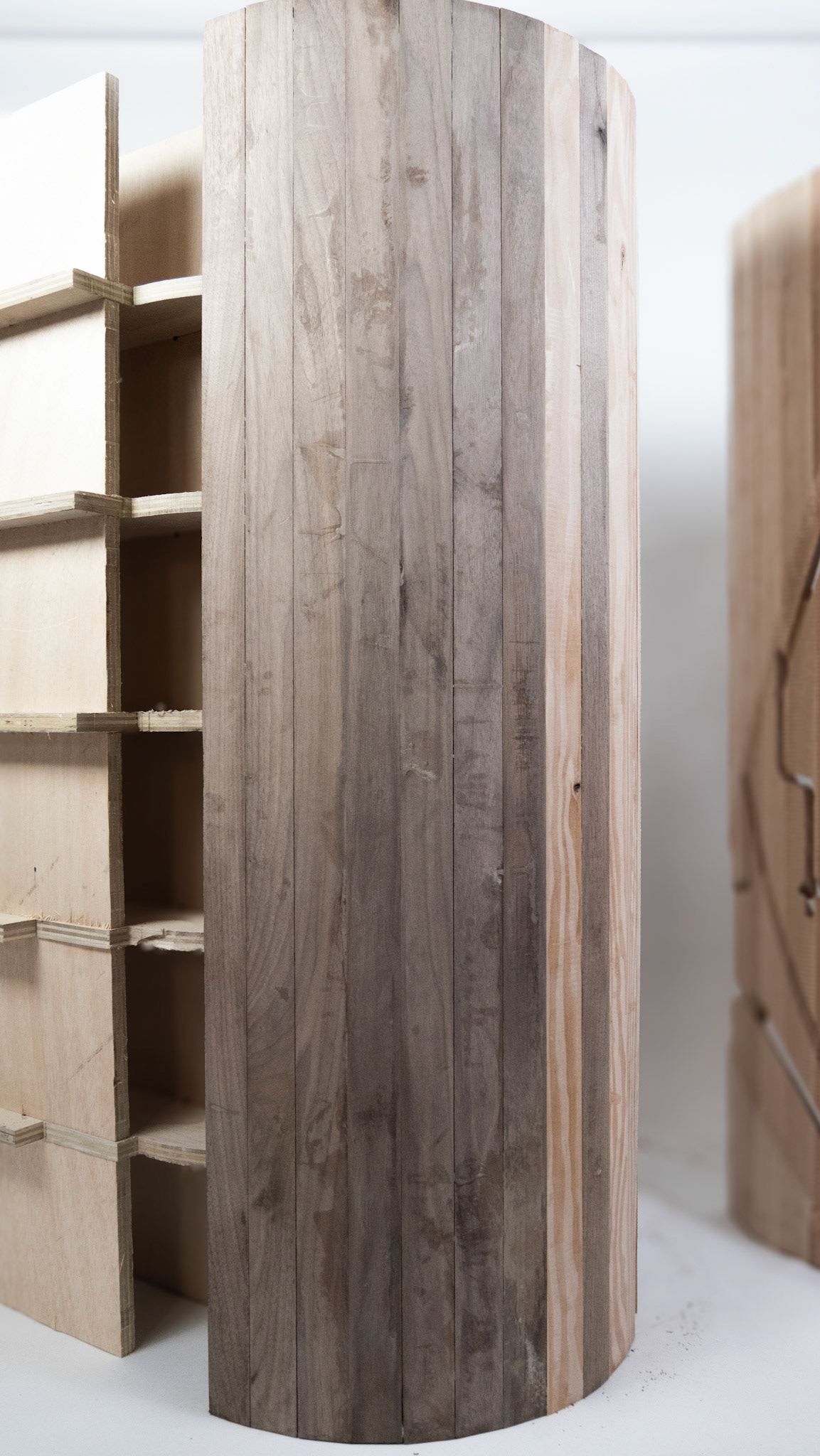
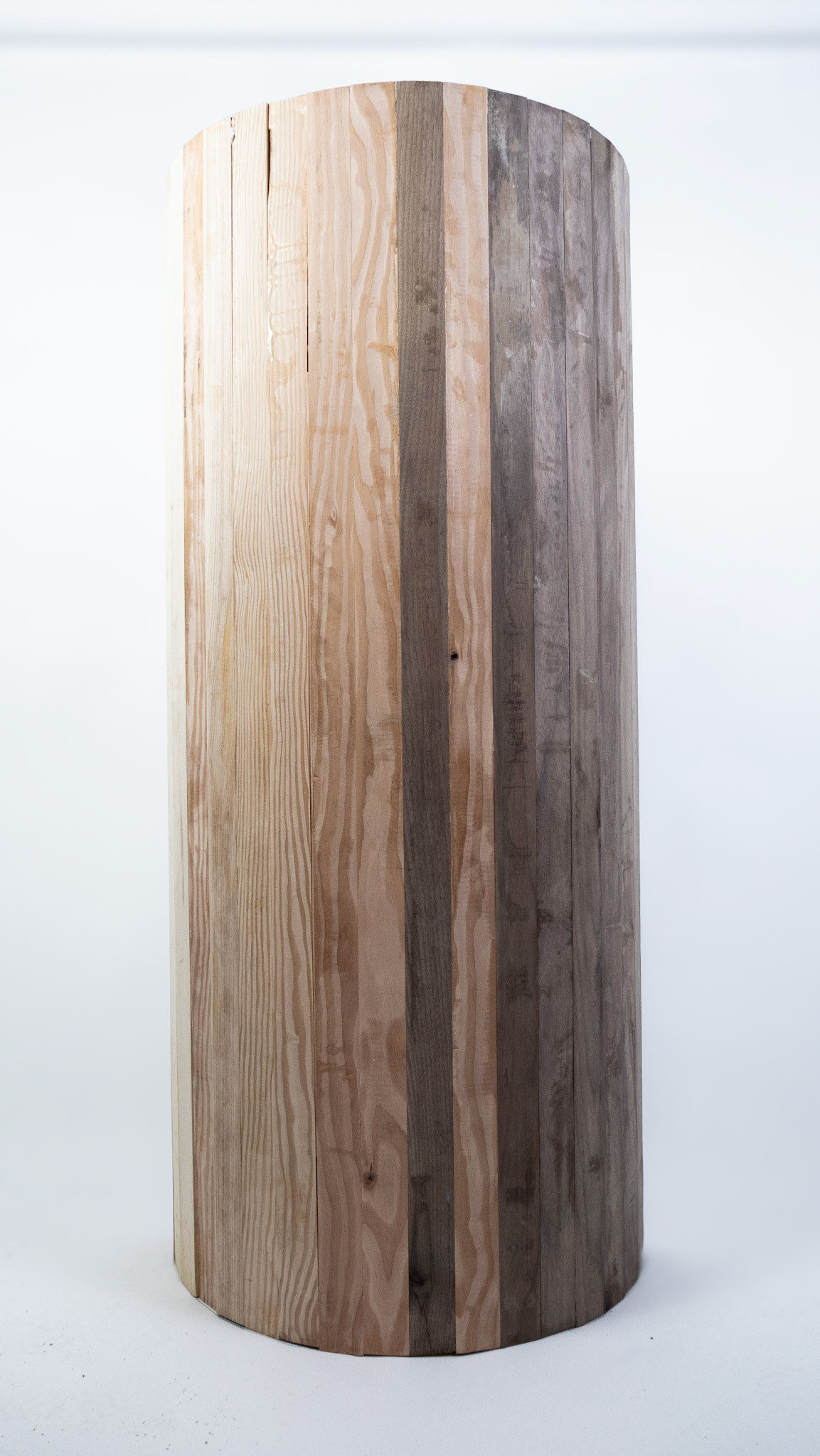
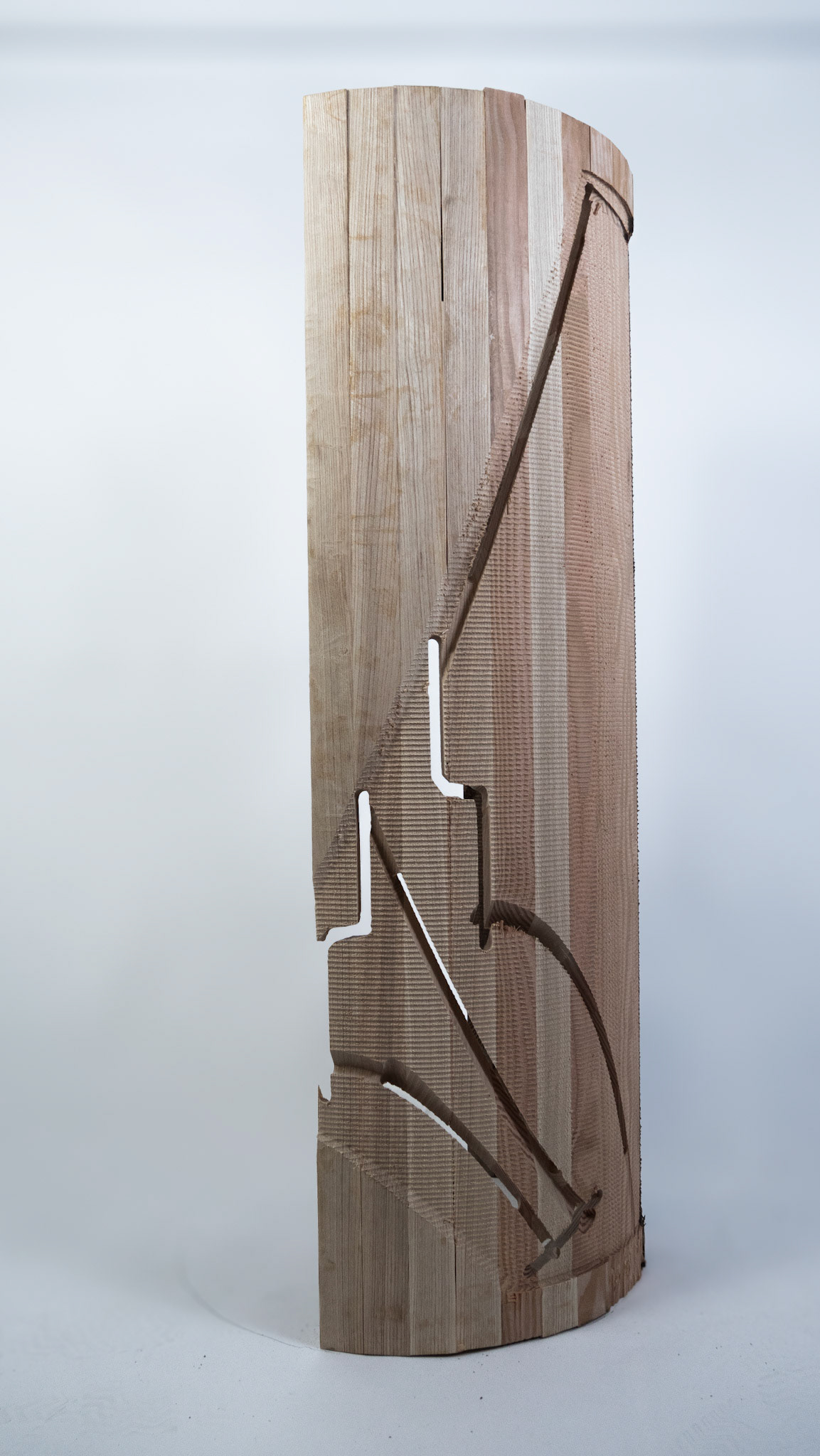
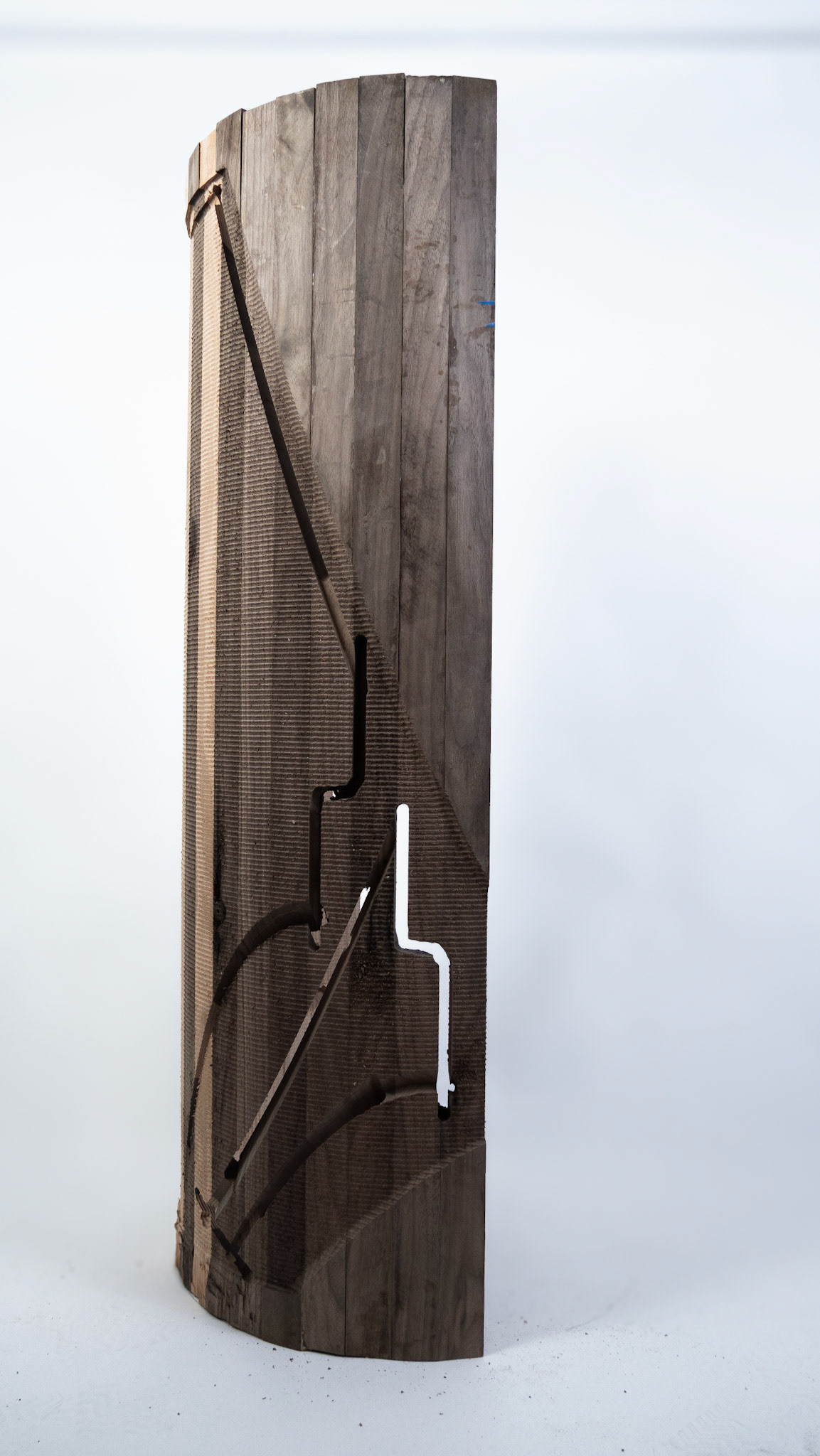
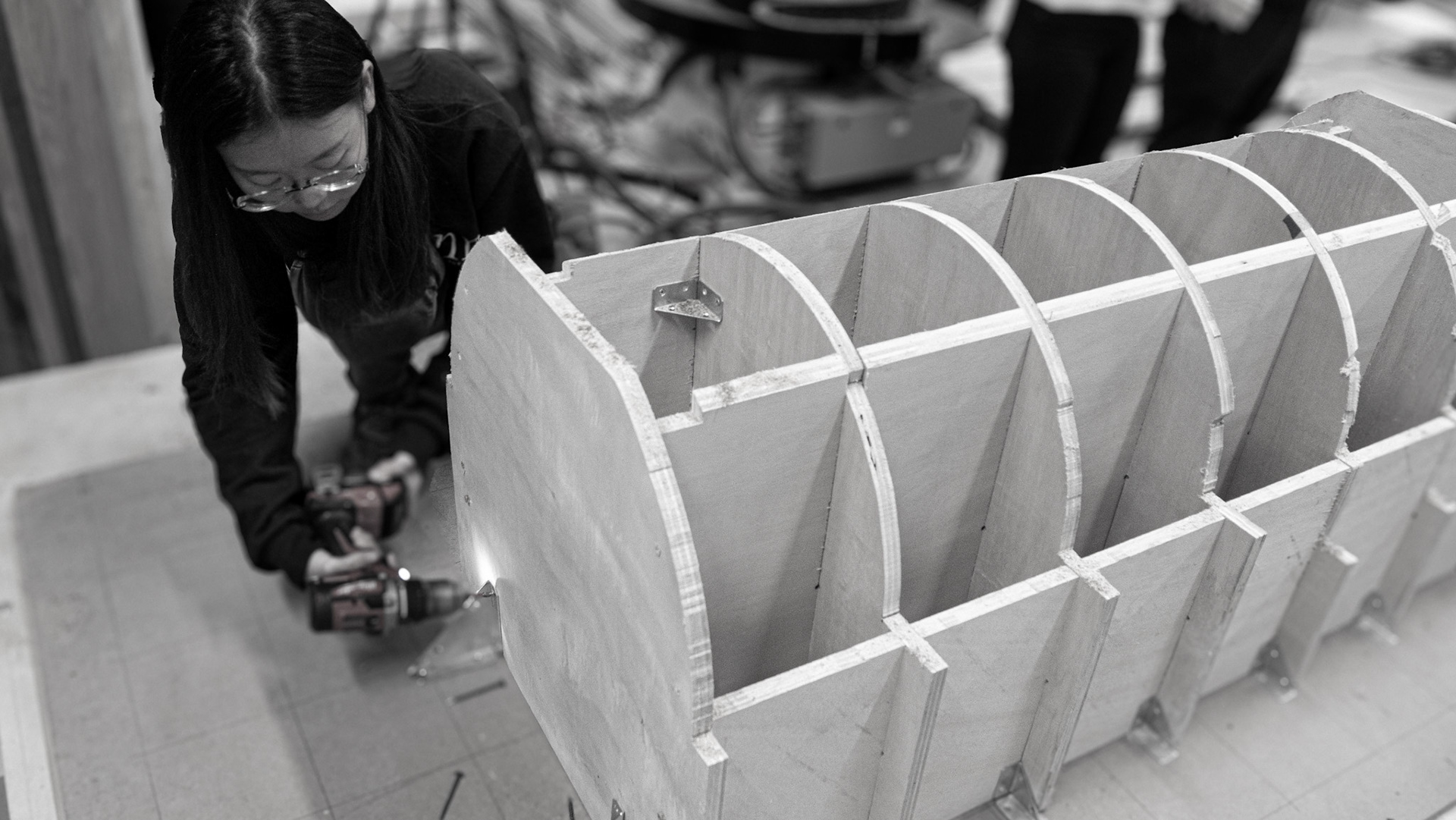
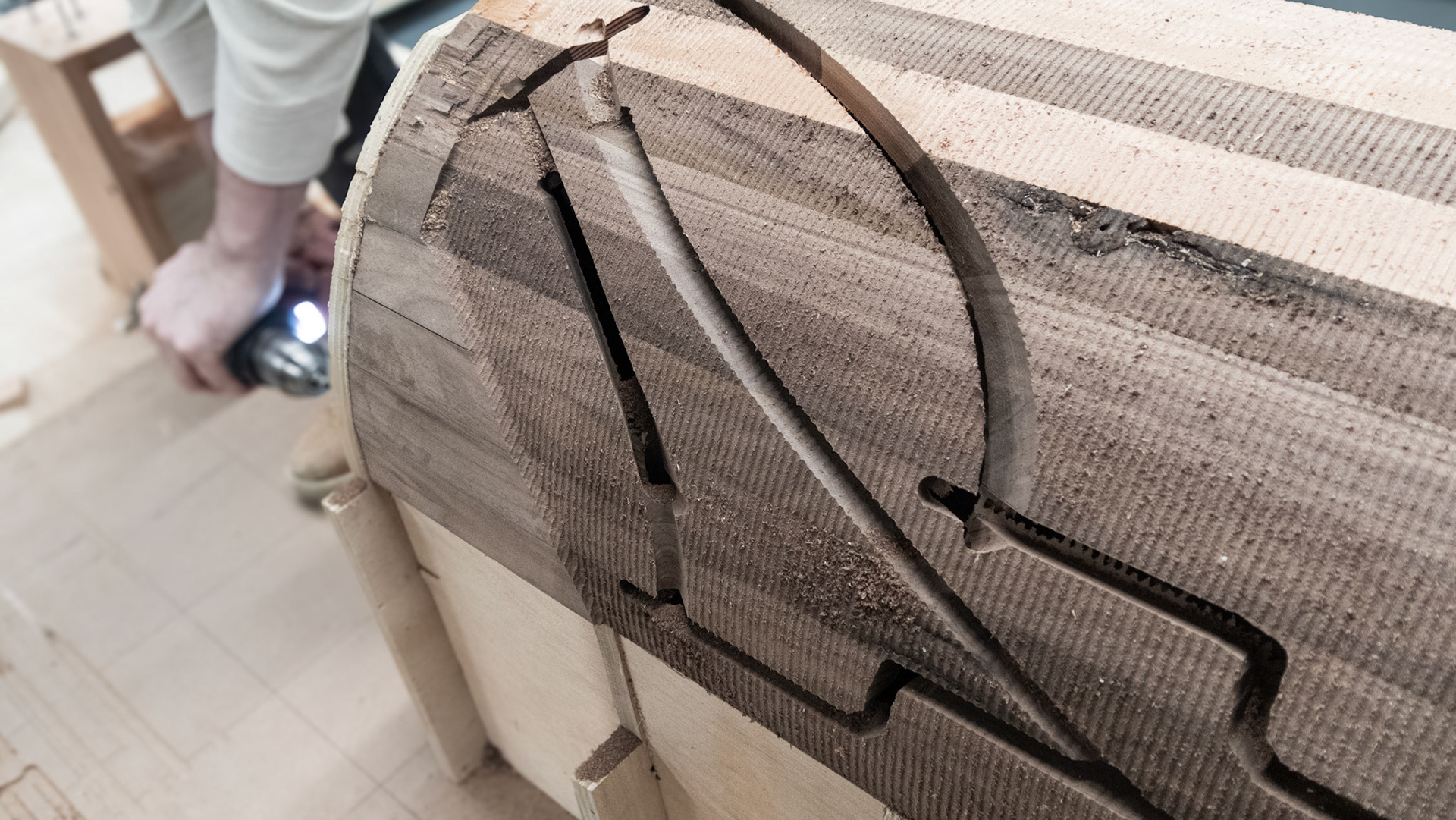
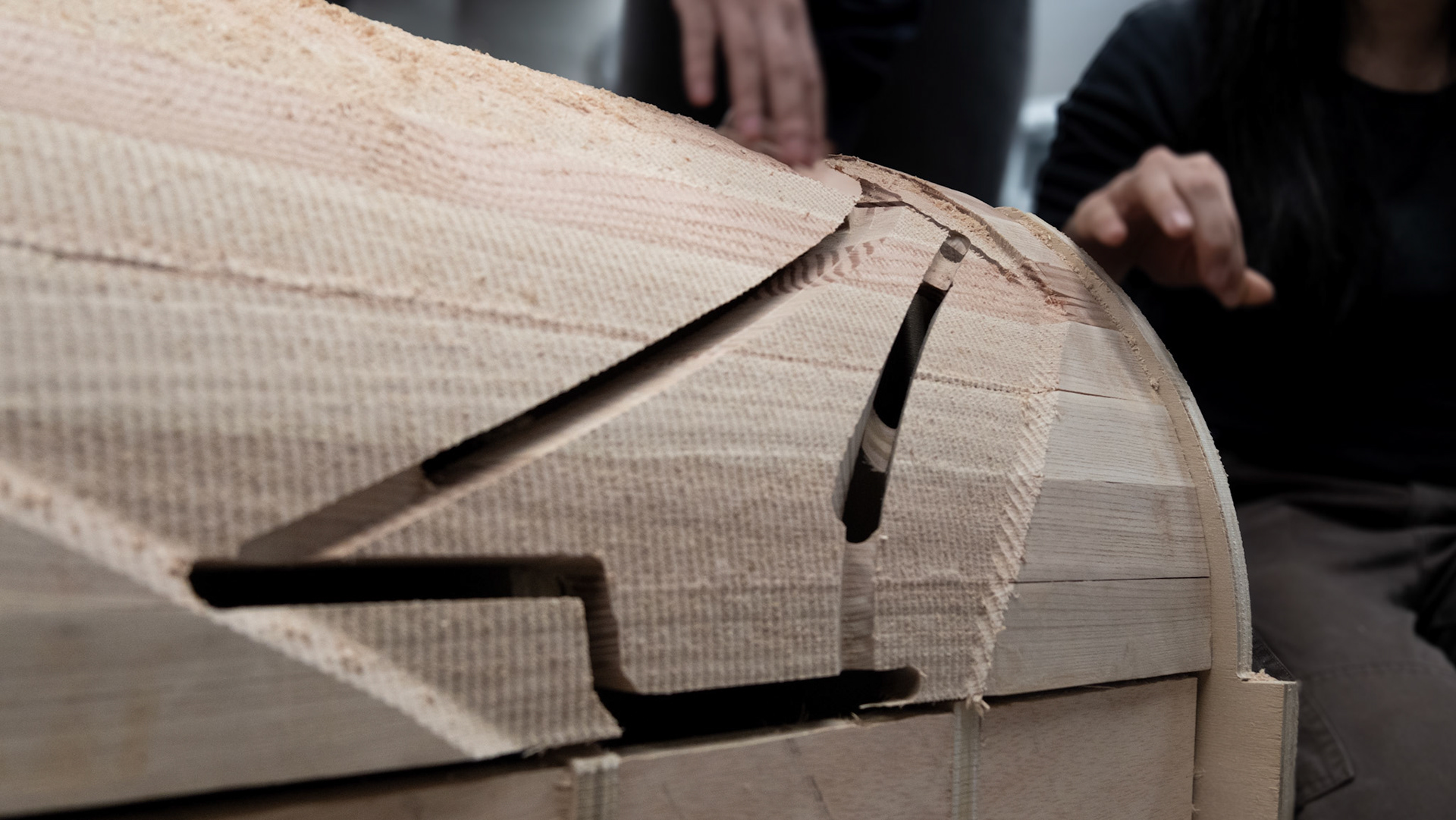
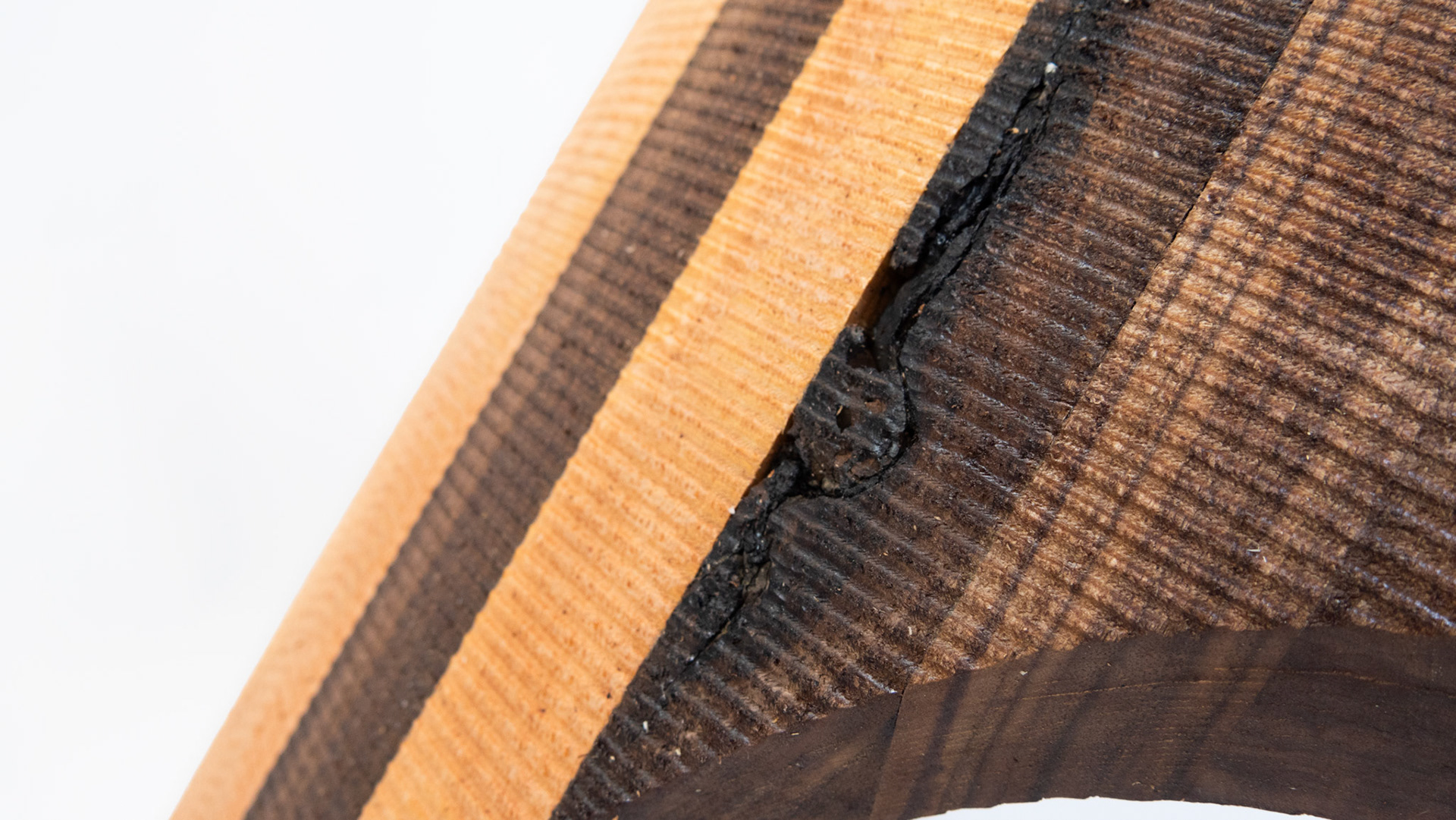

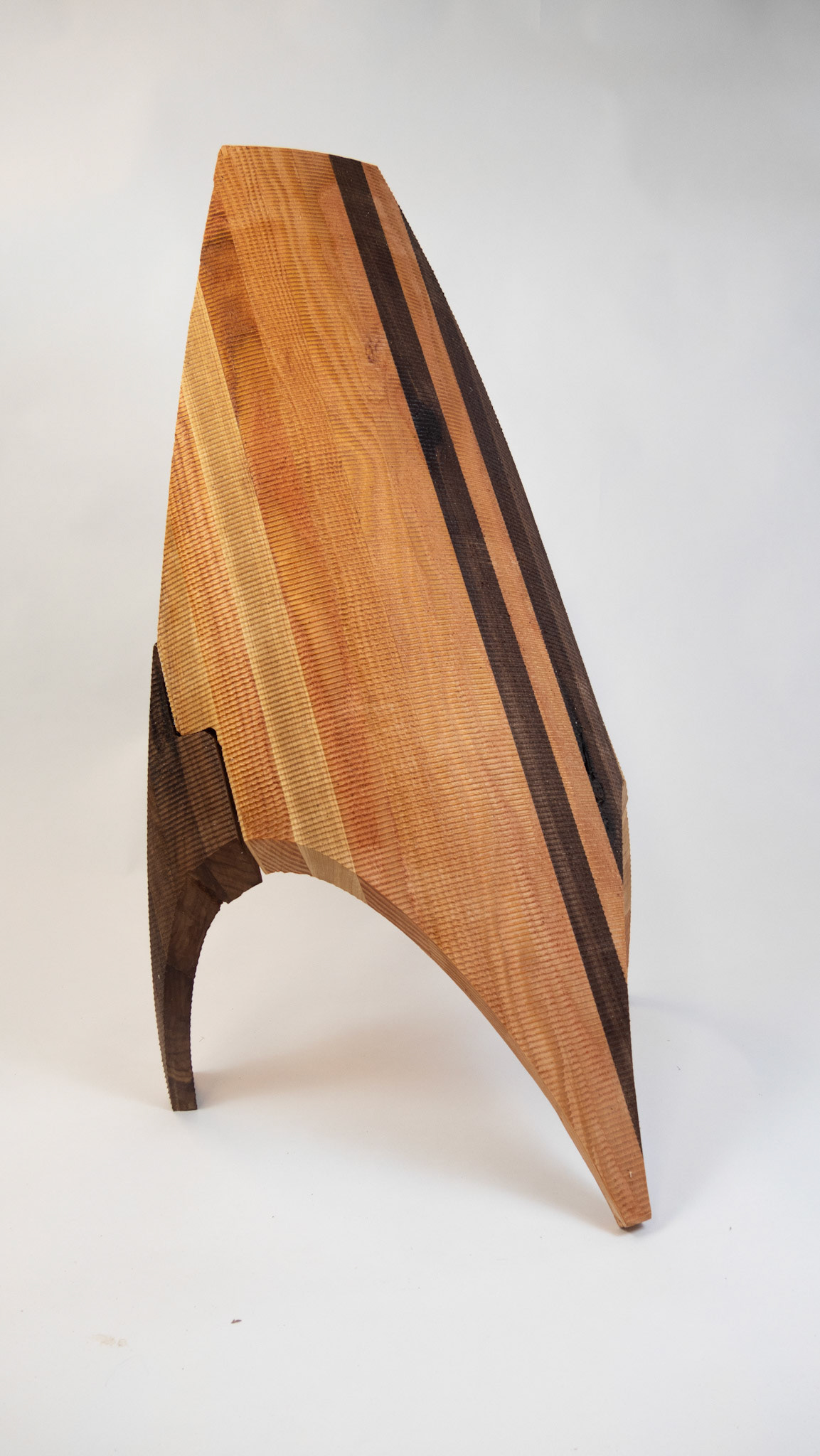
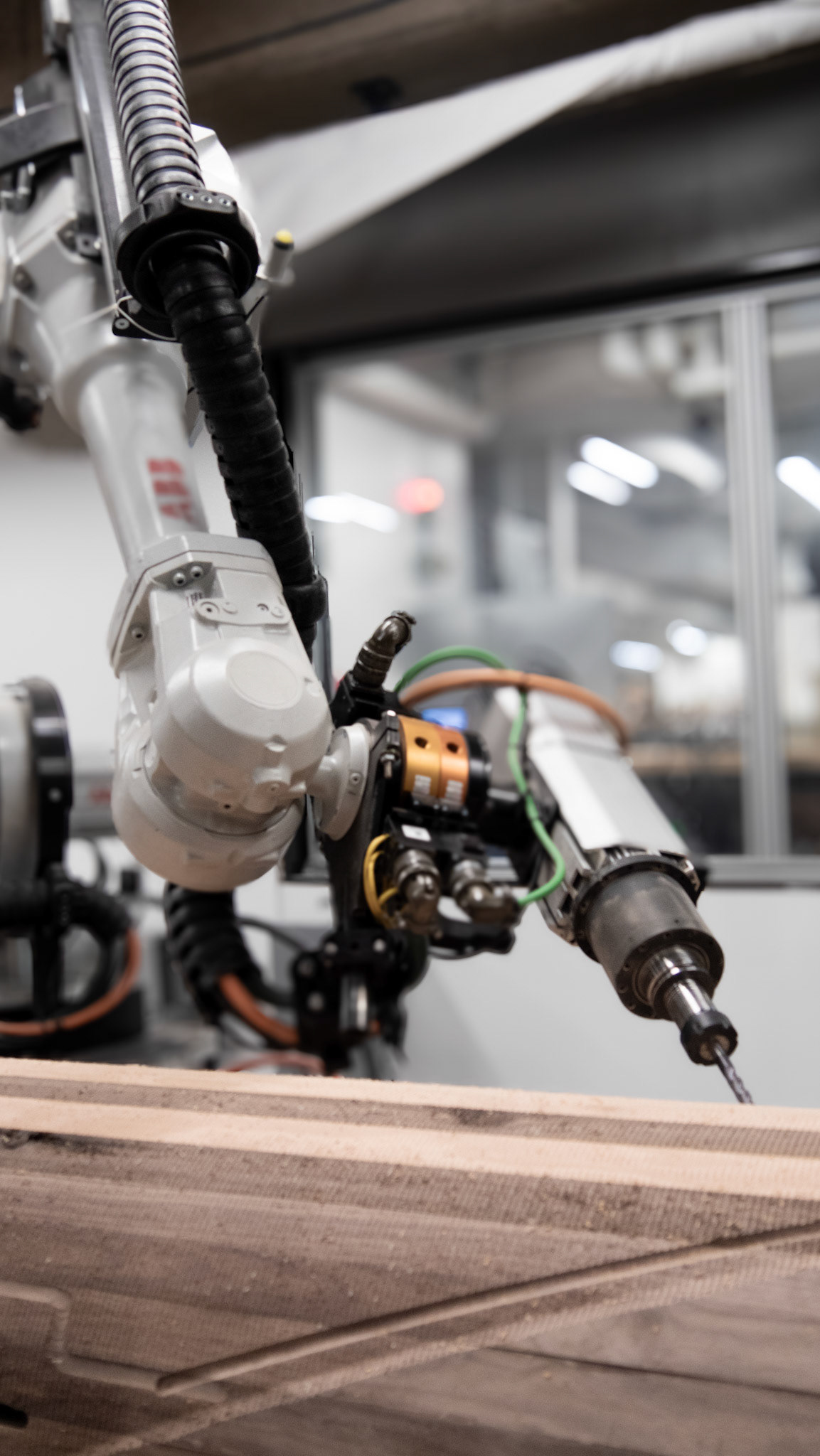
[03] robotic Fabrication - Path Planing
Using Grasshopper, the tools paths were created. For each piece, we needed an outer finishing path, an inner finishing path, and a profile cut.
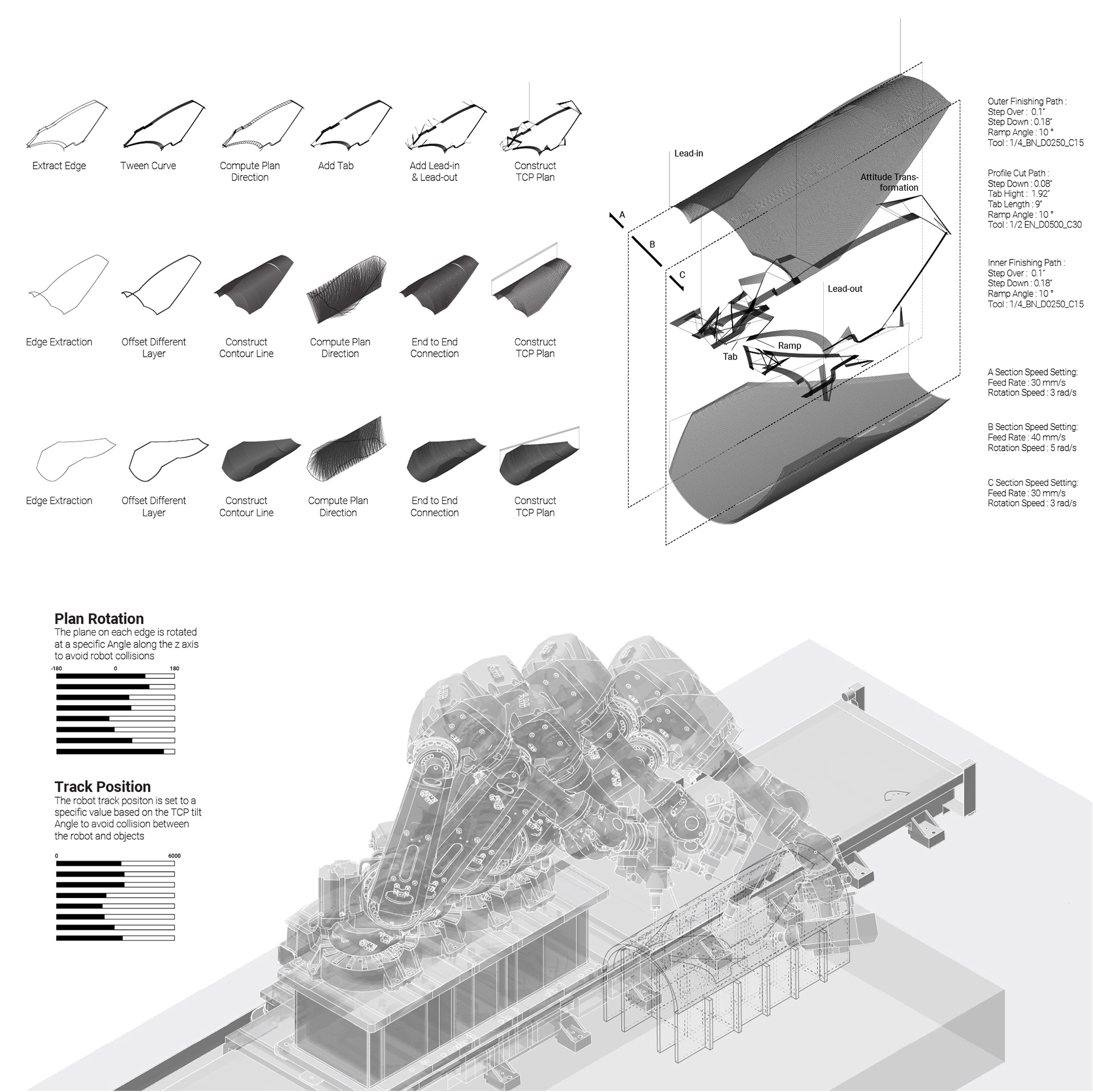
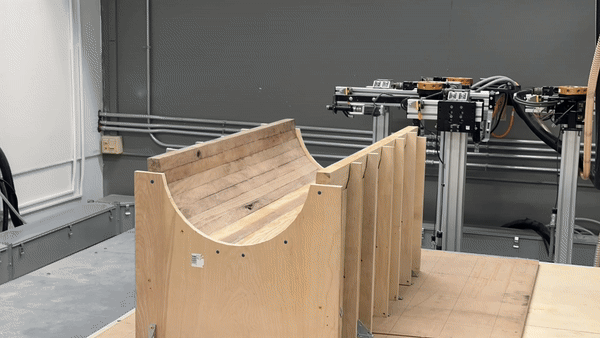
Inner Finishing Path
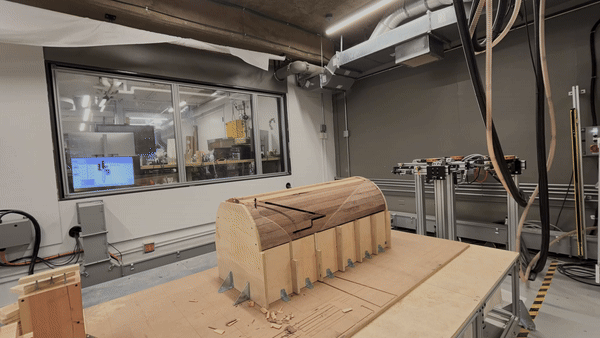
Profile cut path
[04] Machine Learning:
Machine learning could quickly approximate complex functions without the need to construct them manually. To predict the type and dimensions of wood, we need to build a function that can take 20 audio feature values as input and output 4 values: the material type and its length, width, and height.
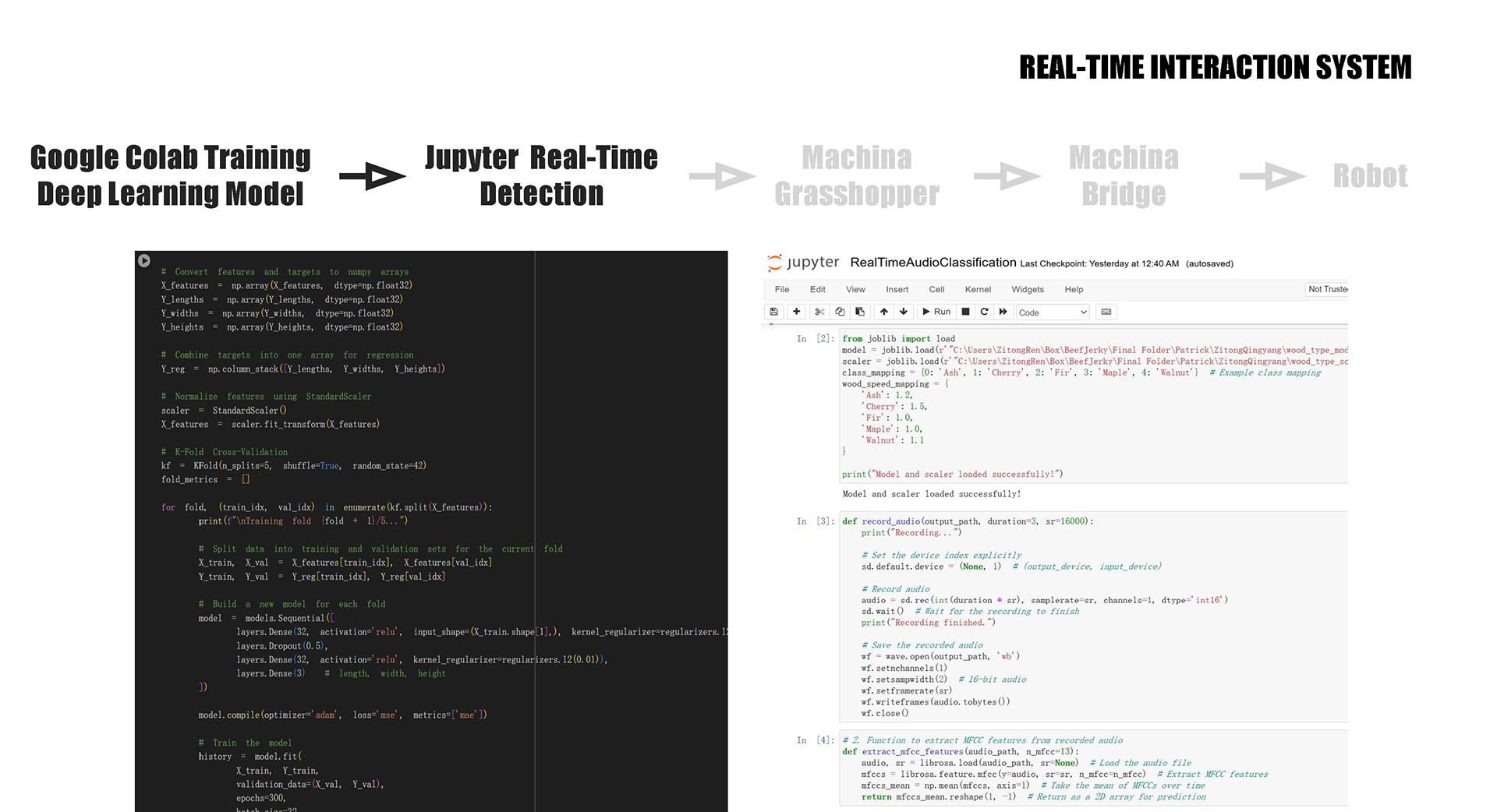

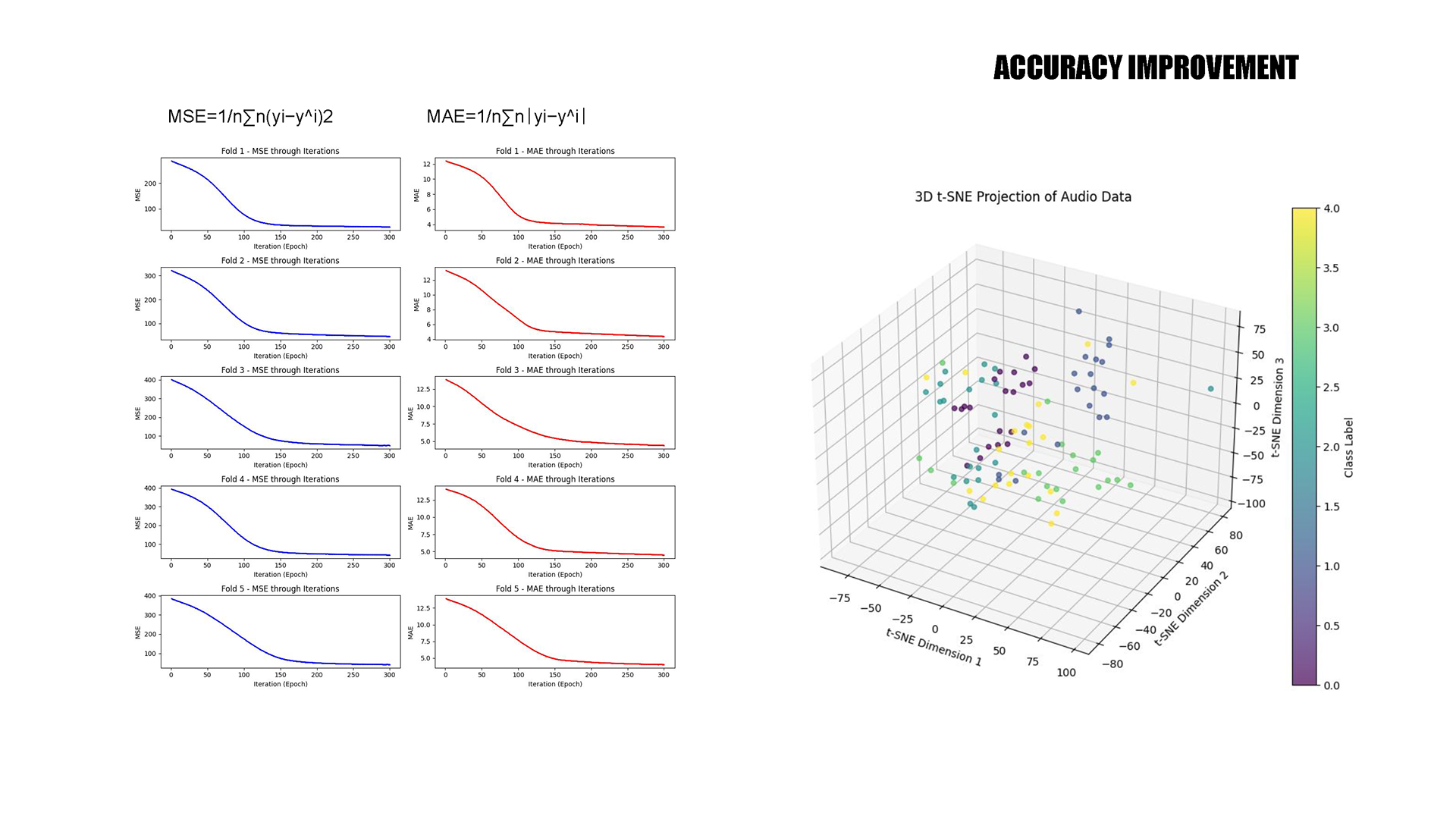
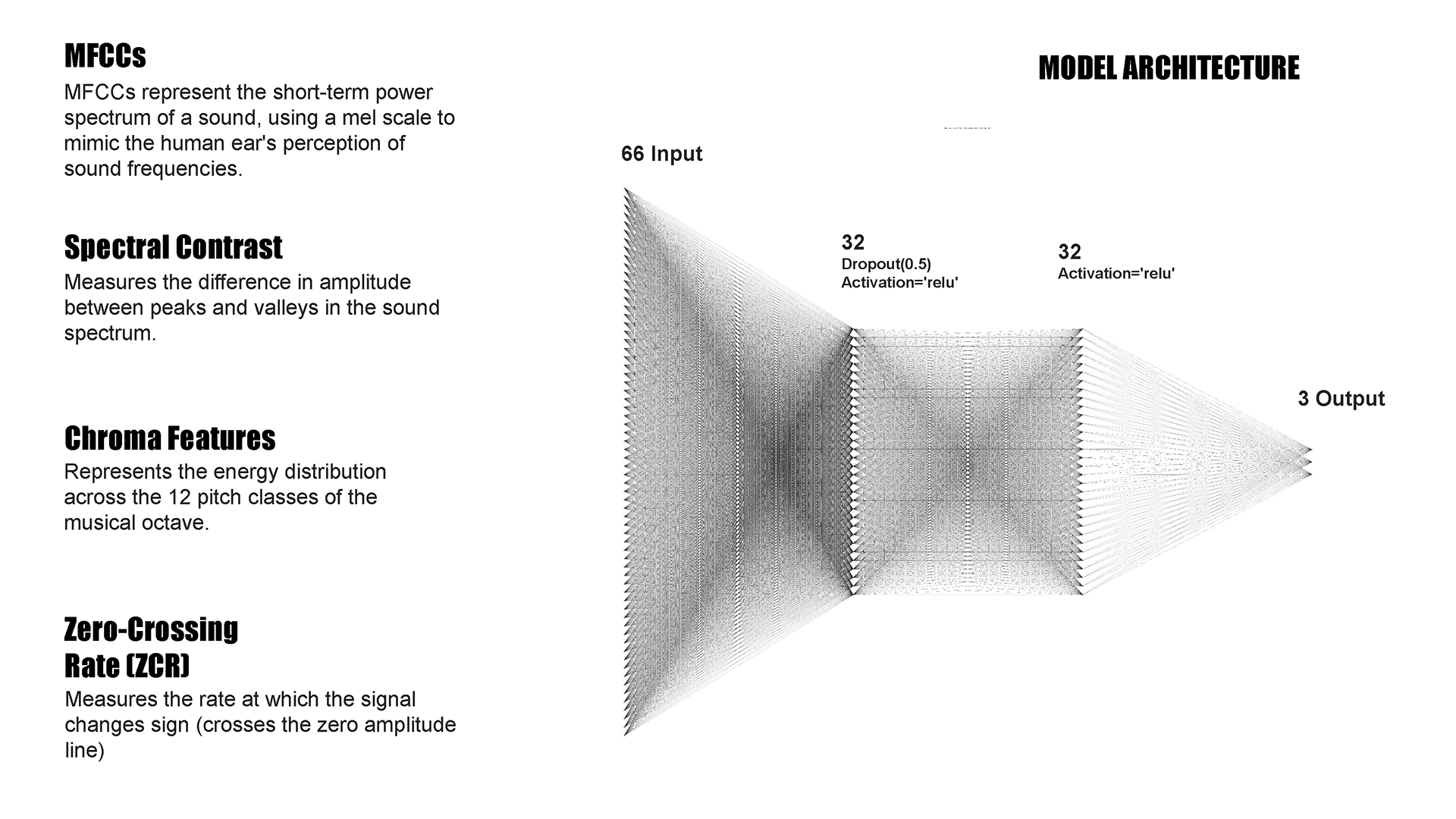
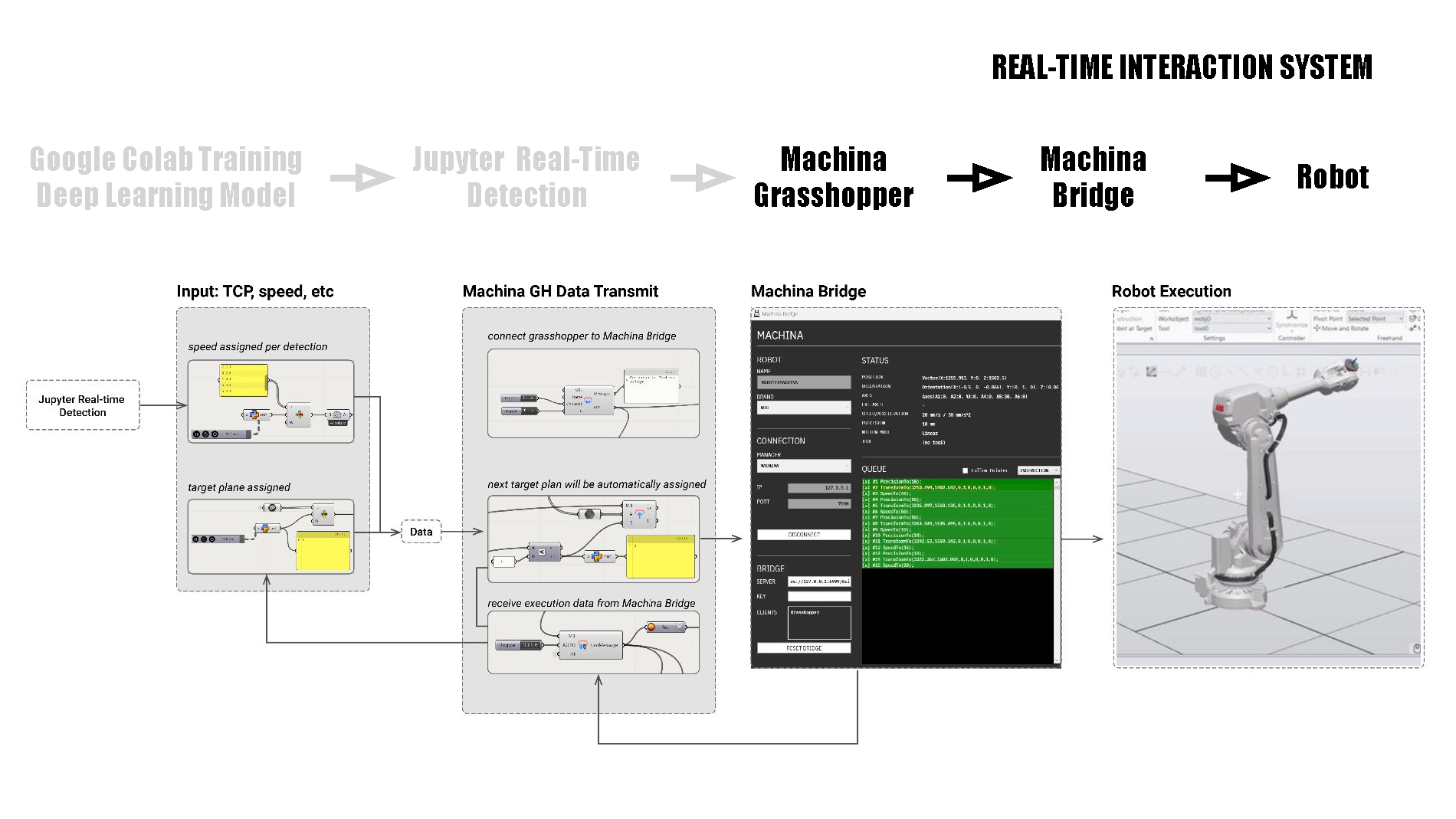