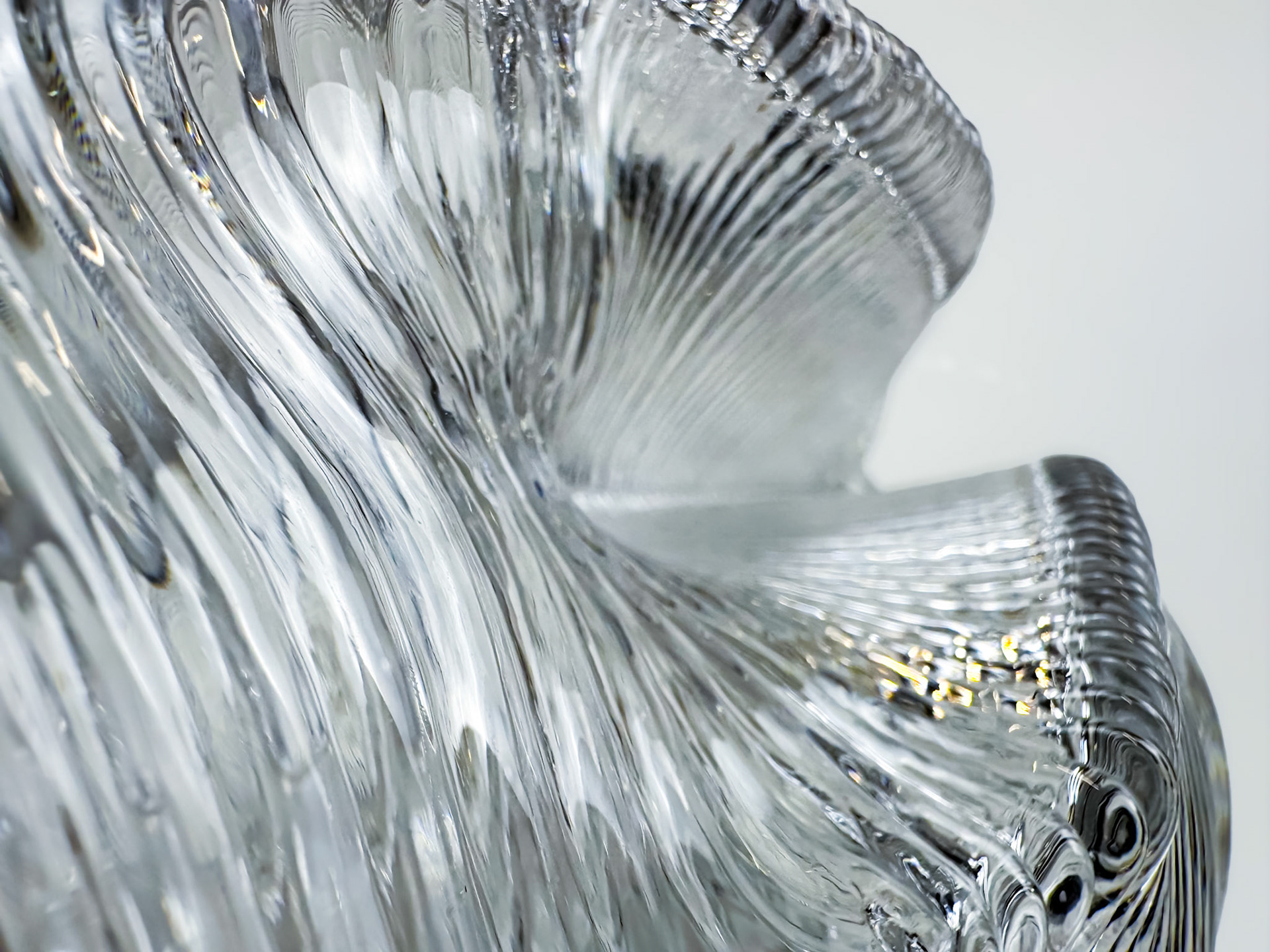
Robotic Fused Granular Fabrication
Robotic Fused Granular Fabrication (FGF) Blow-forming explores the intersection of additive manufacturing, robotic fabrication, and material behavior. This process integrates granular extrusion-based 3D printing with robotic forming techniques to shape complex geometries dynamically.
The research focuses on real-time material manipulation, using robotic arms to extrude thermoplastics while simultaneously introducing controlled air pressure to expand and deform the printed form. This approach enables lightweight, structurally optimized, and materially efficient architectural components, pushing the boundaries of robotic fabrication in design.
Key explorations include:
Material Flow & Extrusion Dynamics – Understanding thermoplastic rheology in FGF
Multi-Axis Robotic Control – Synchronous toolpath programming for printing and blow forming
Structural Optimization – Generative and performance-based design strategies
Hybrid Fabrication Techniques – Integrating heat-based forming with additive manufacturing
This research contributes to the broader discourse on sustainable digital fabrication, emphasizing material circularity, waste reduction, and performance-driven design strategies.
Institution: University of Pennsylvania
Lab: Advanced Research and Innovation lab
Instructor: Robert Stuart-Smith, Nathan King, Laia Mogas-Soldevila, Jeffrey Anderson
Graduate Teaching Assistants: Mahsa Masalegoo, Franklin Wu
Lab Managers: Nicholas Sideropoulos, Shunta Moriuchi
In Collaboration with: Zitong Ren, Burcu Gocen, Qingyang Xu.
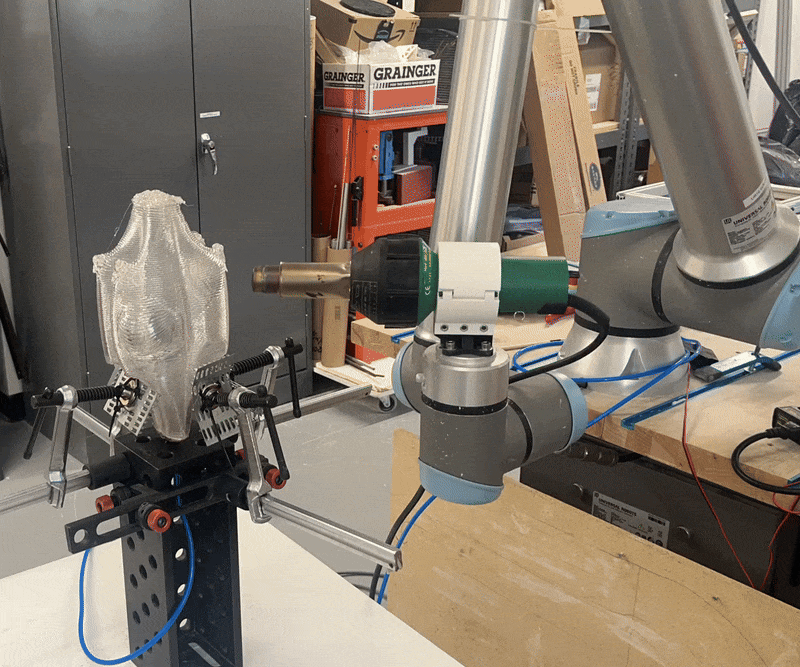
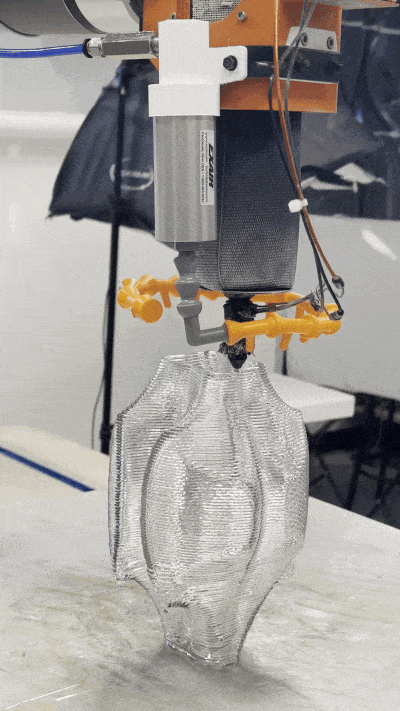
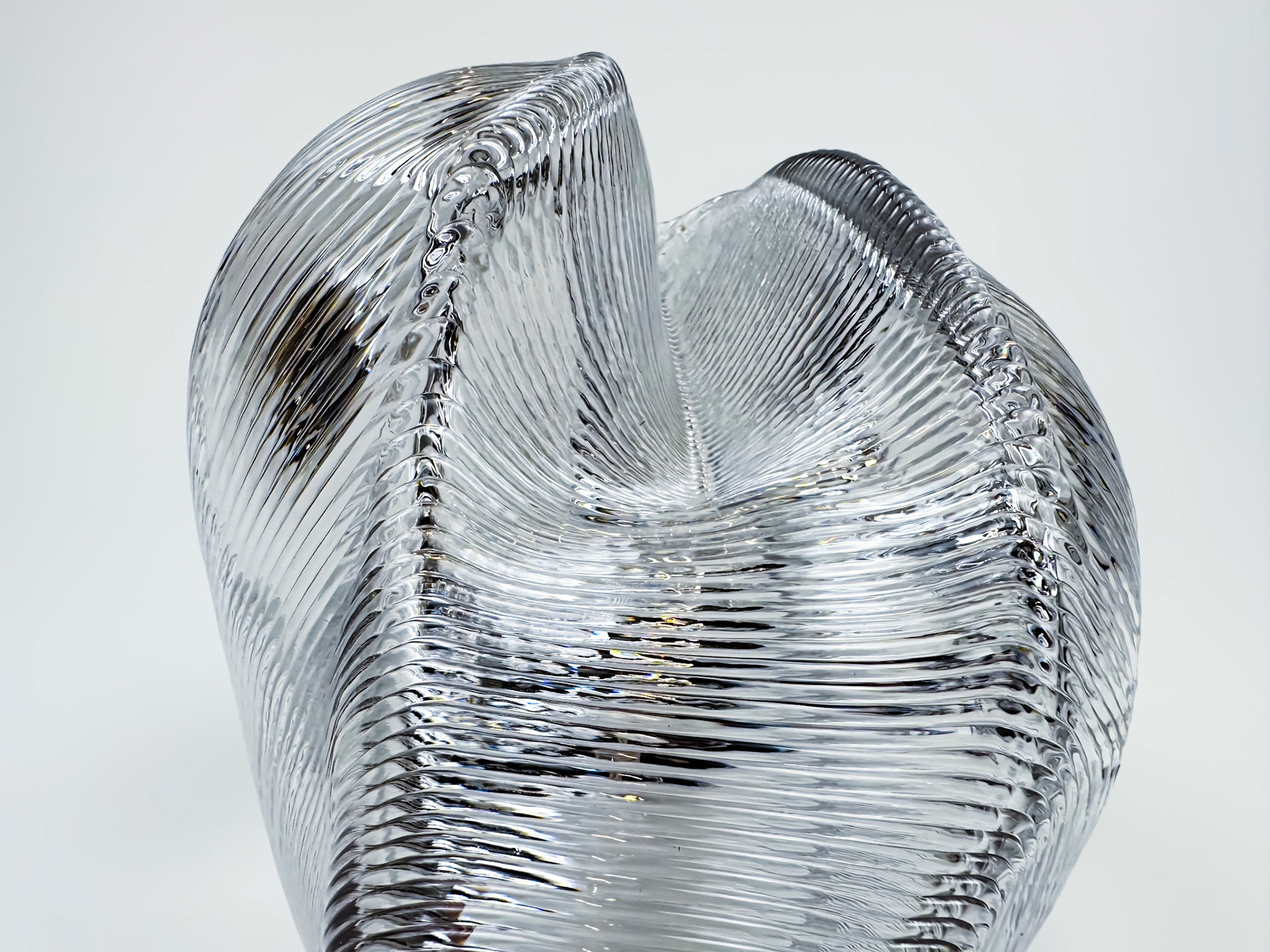
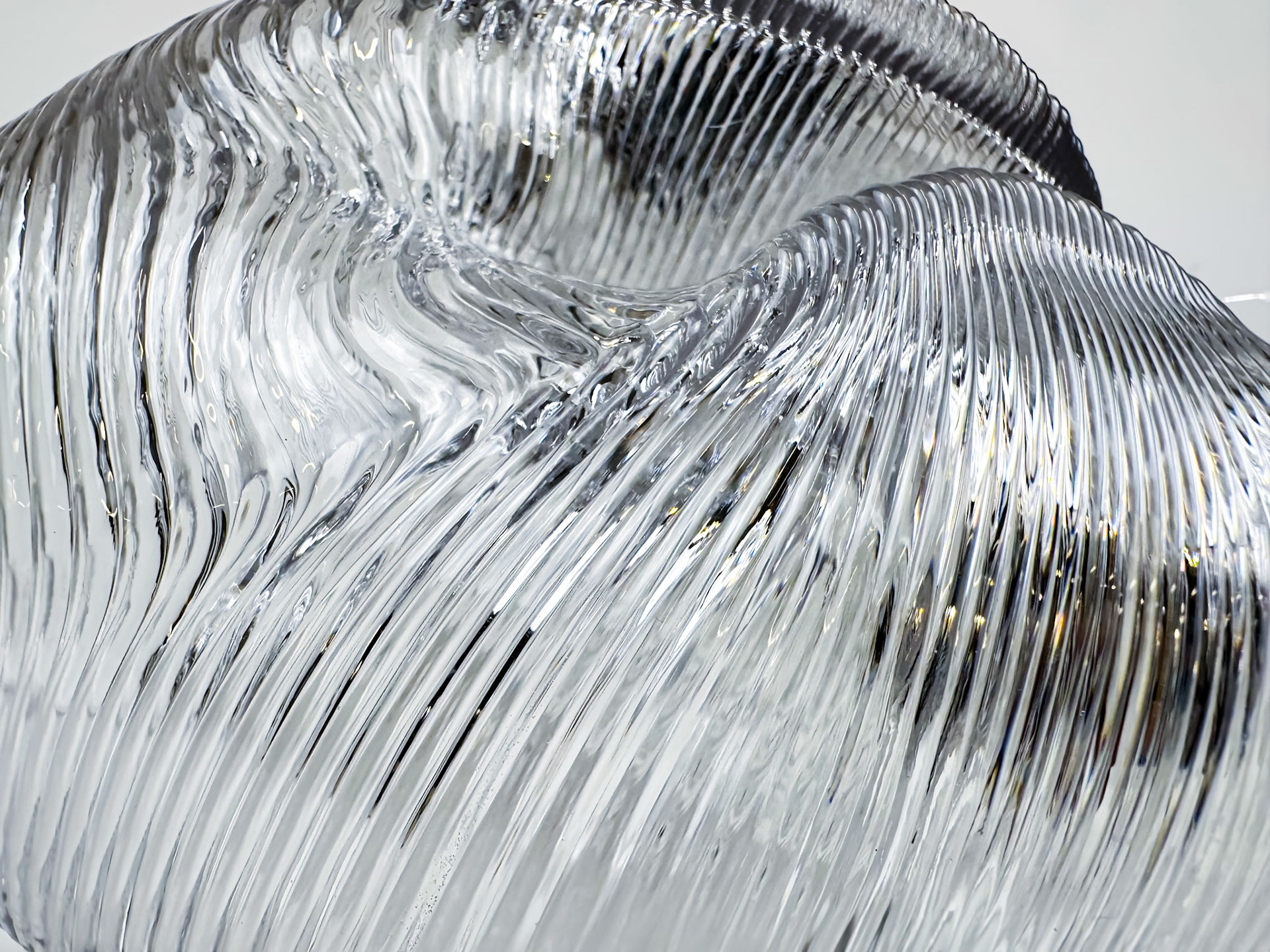
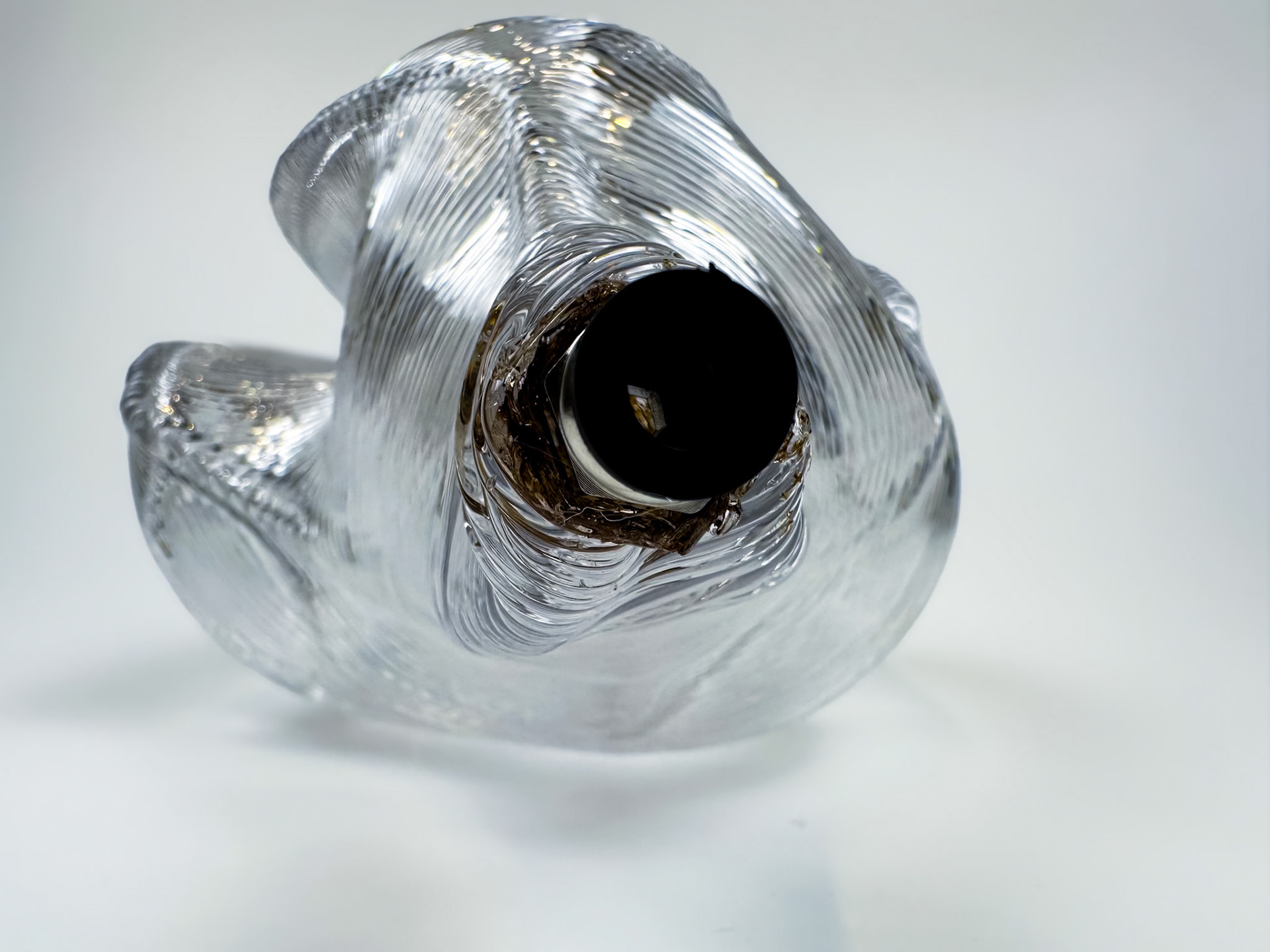
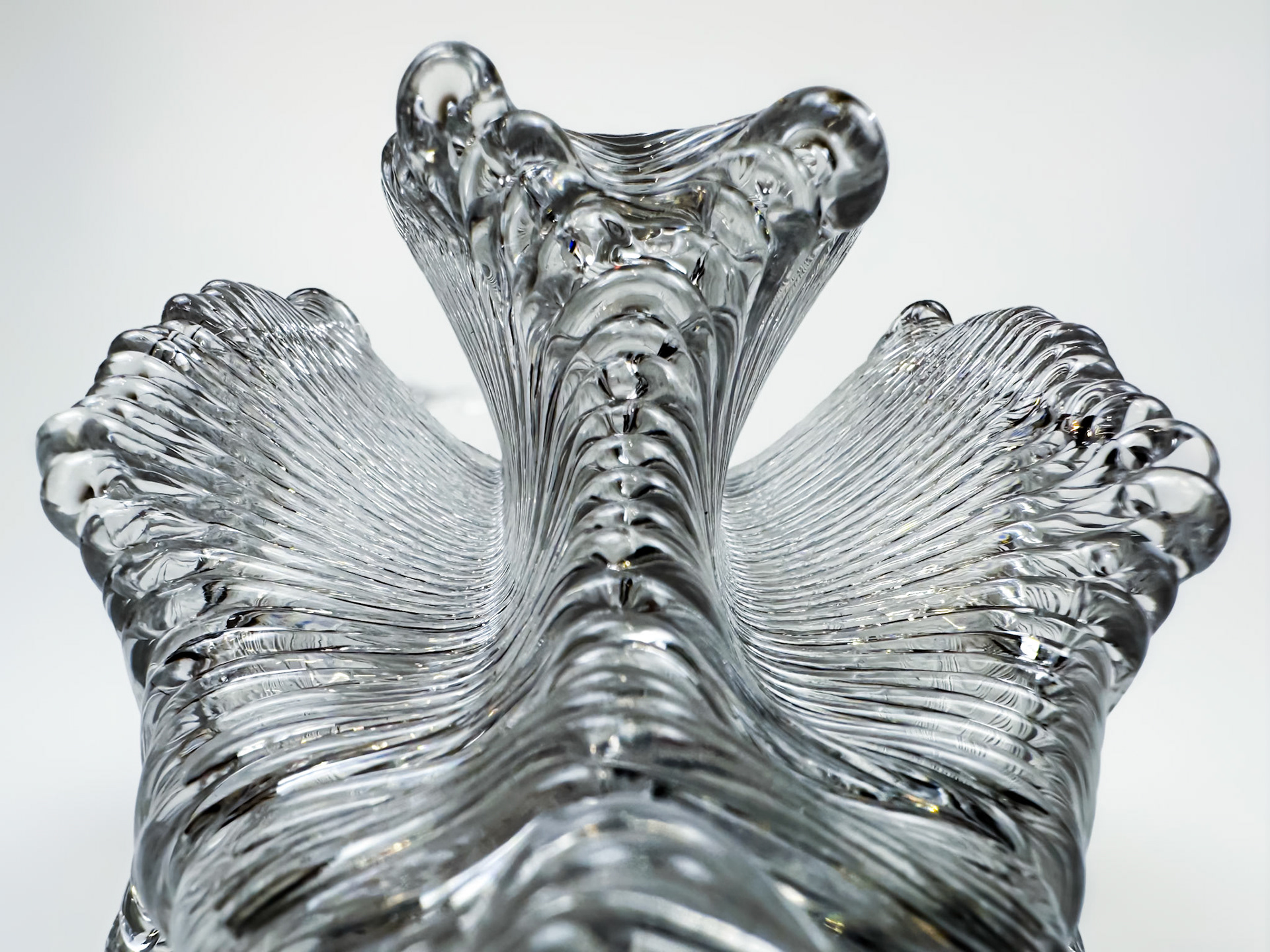
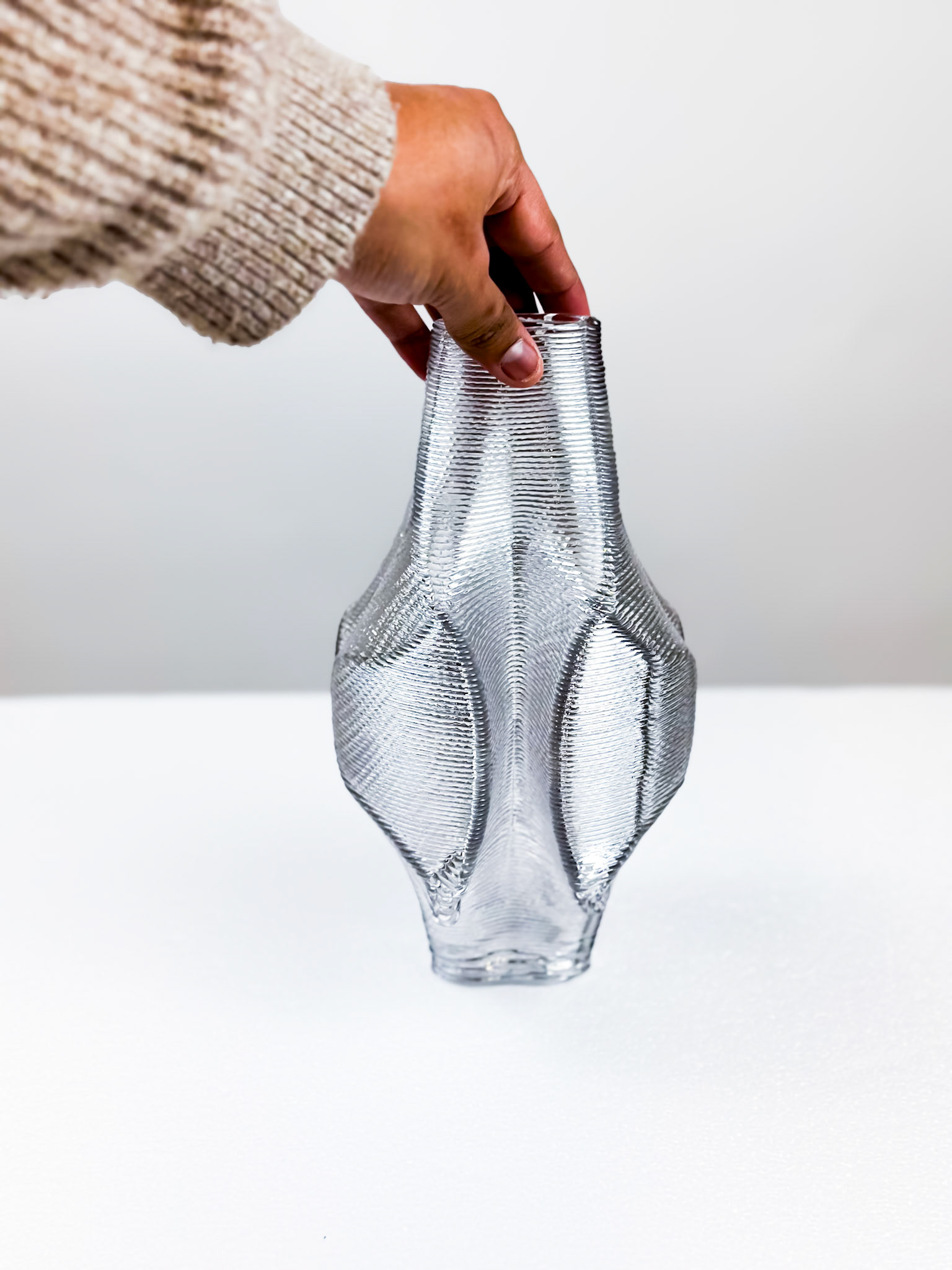
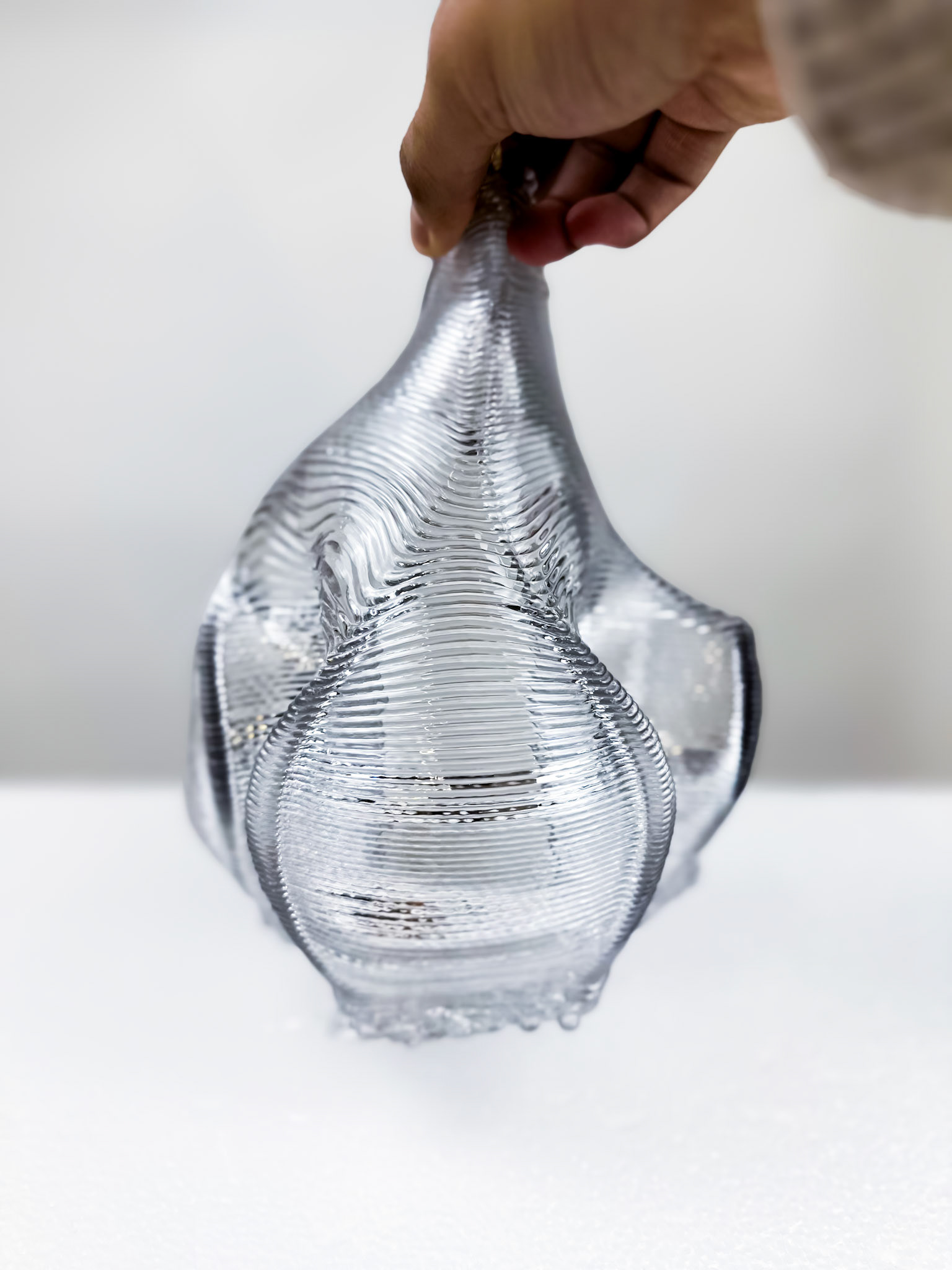
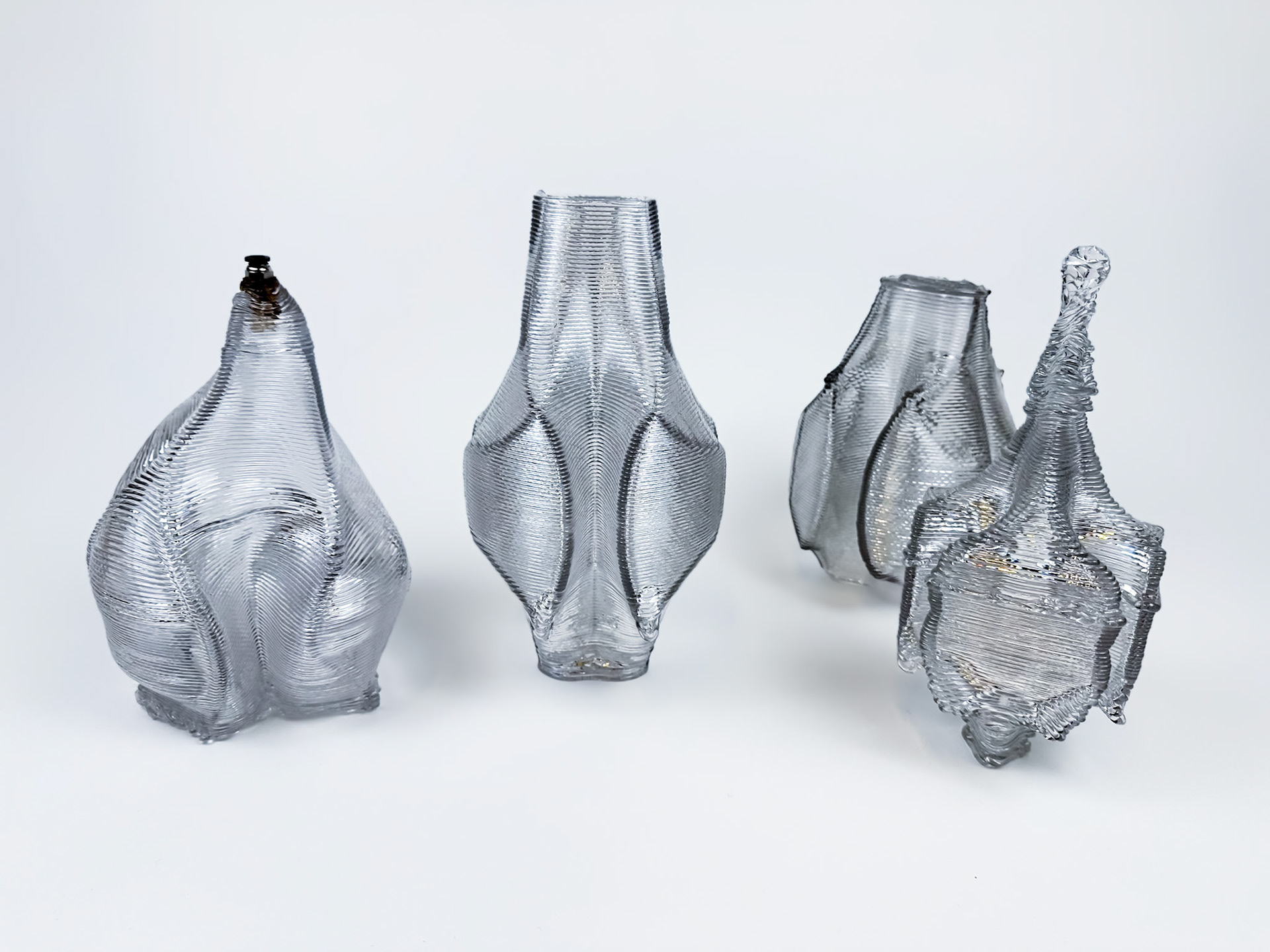
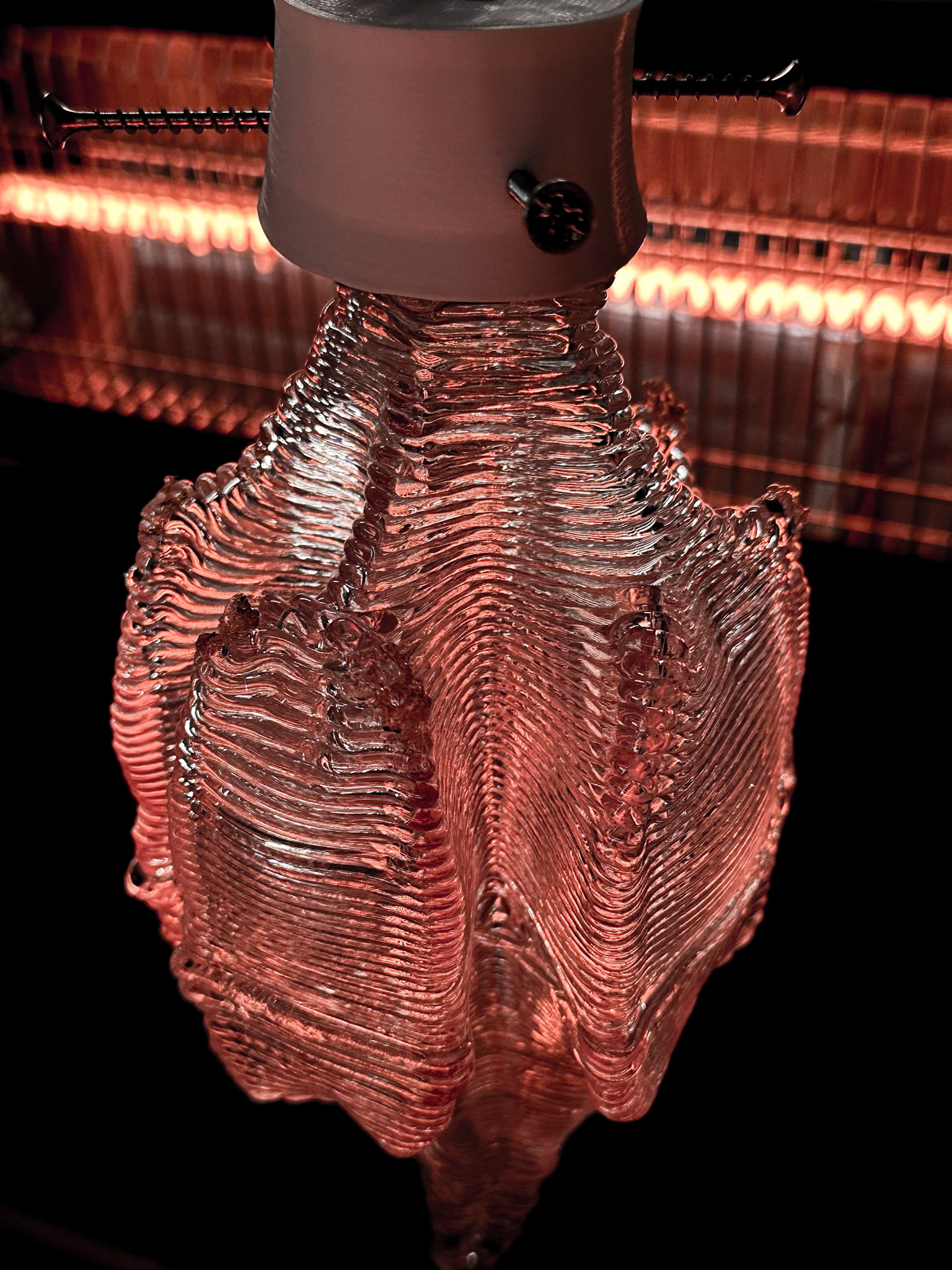
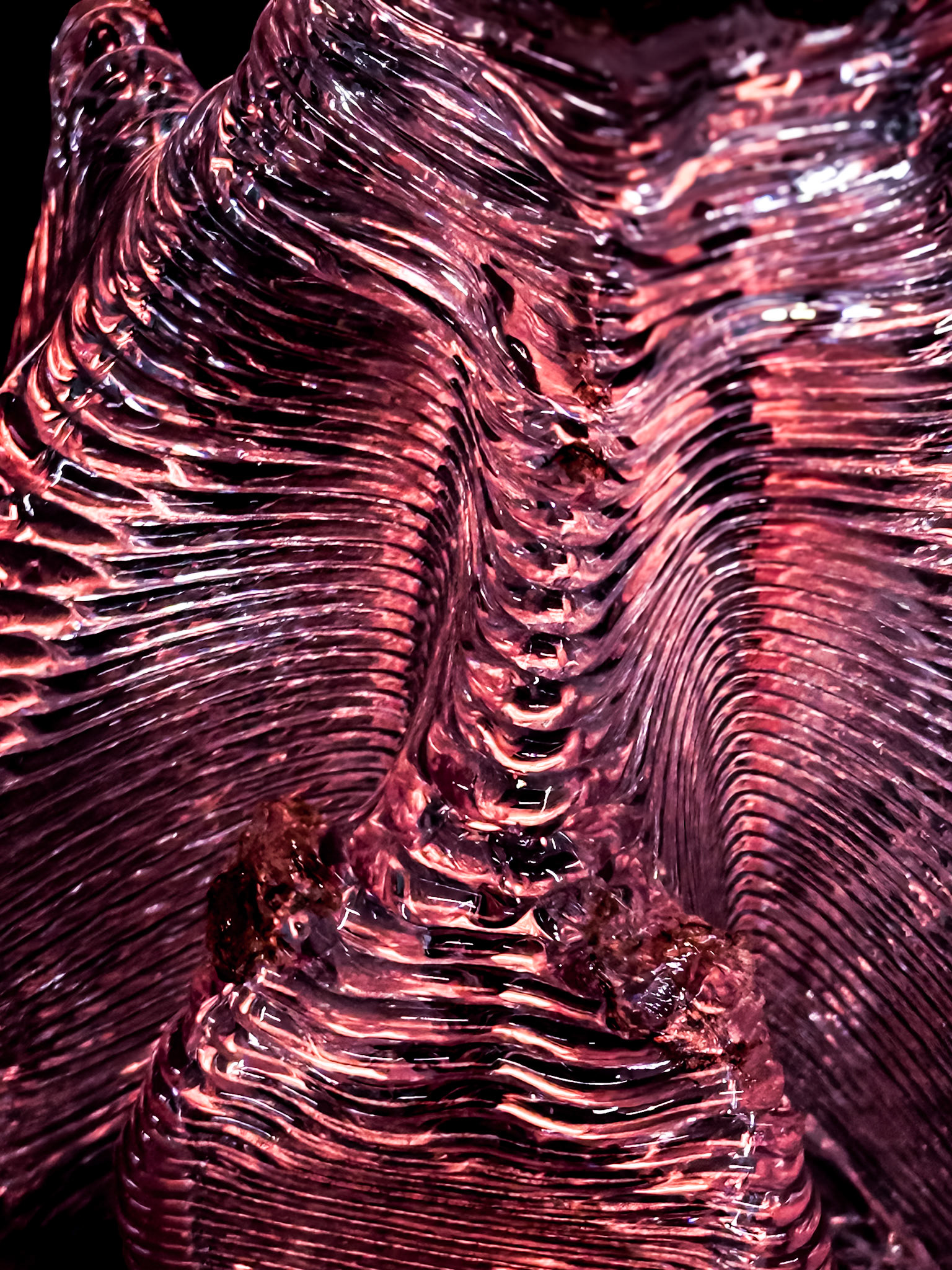
Interlocking Systems through blow-forming.
This research further investigates interlocking systems through blow forming, using simulations to study these conditions before performing physical tests.
The air-blown inflation method, when combined with a jammed structure, offers several advantages:
1) Precise control over node shapes, eliminating distortions caused by layer lines.
2) Increased forming speed compared to 3D printing, producing thin-walled, lightweight components.
3) Complex geometries can be achieved without the need for support structures.
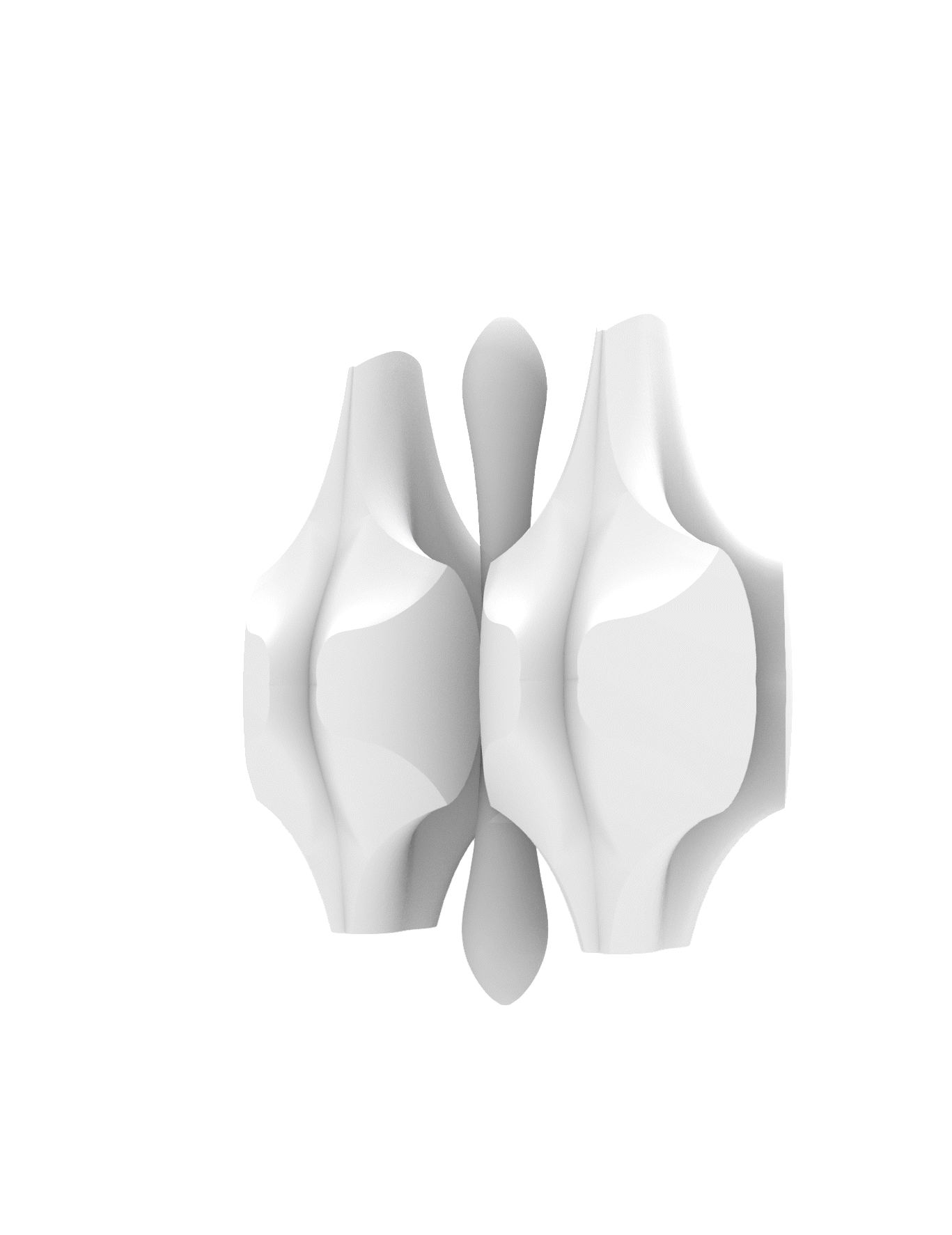
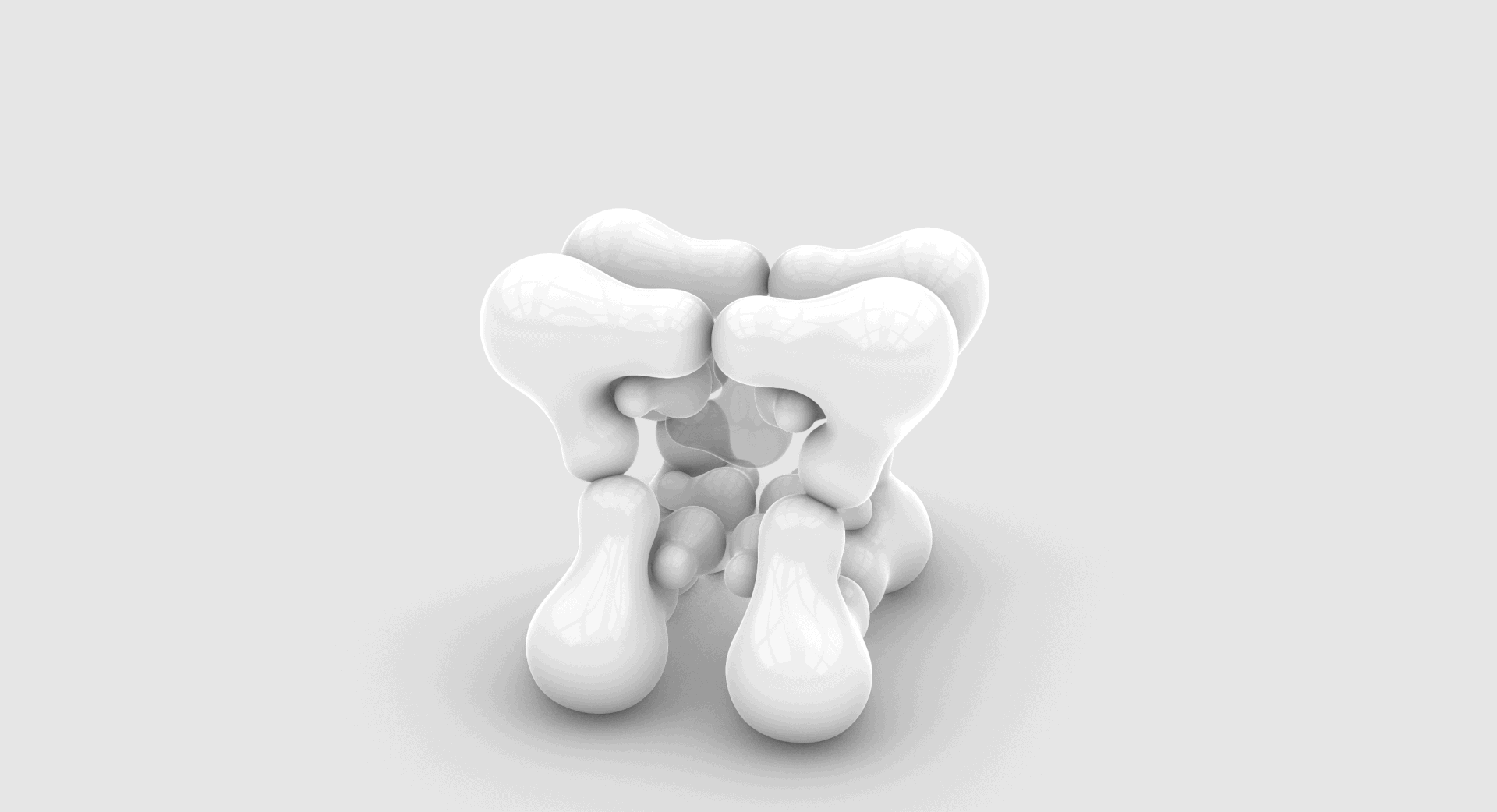
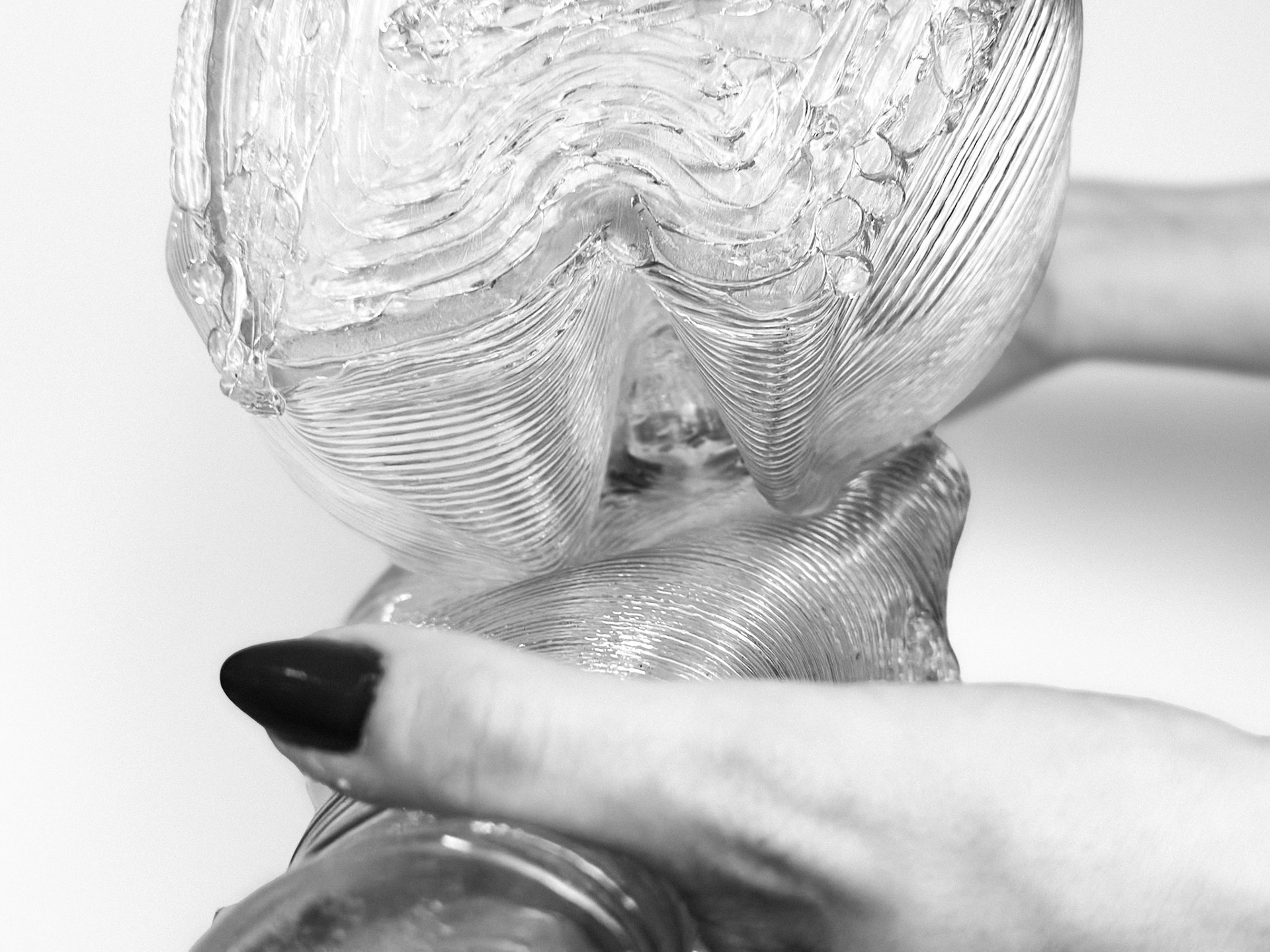
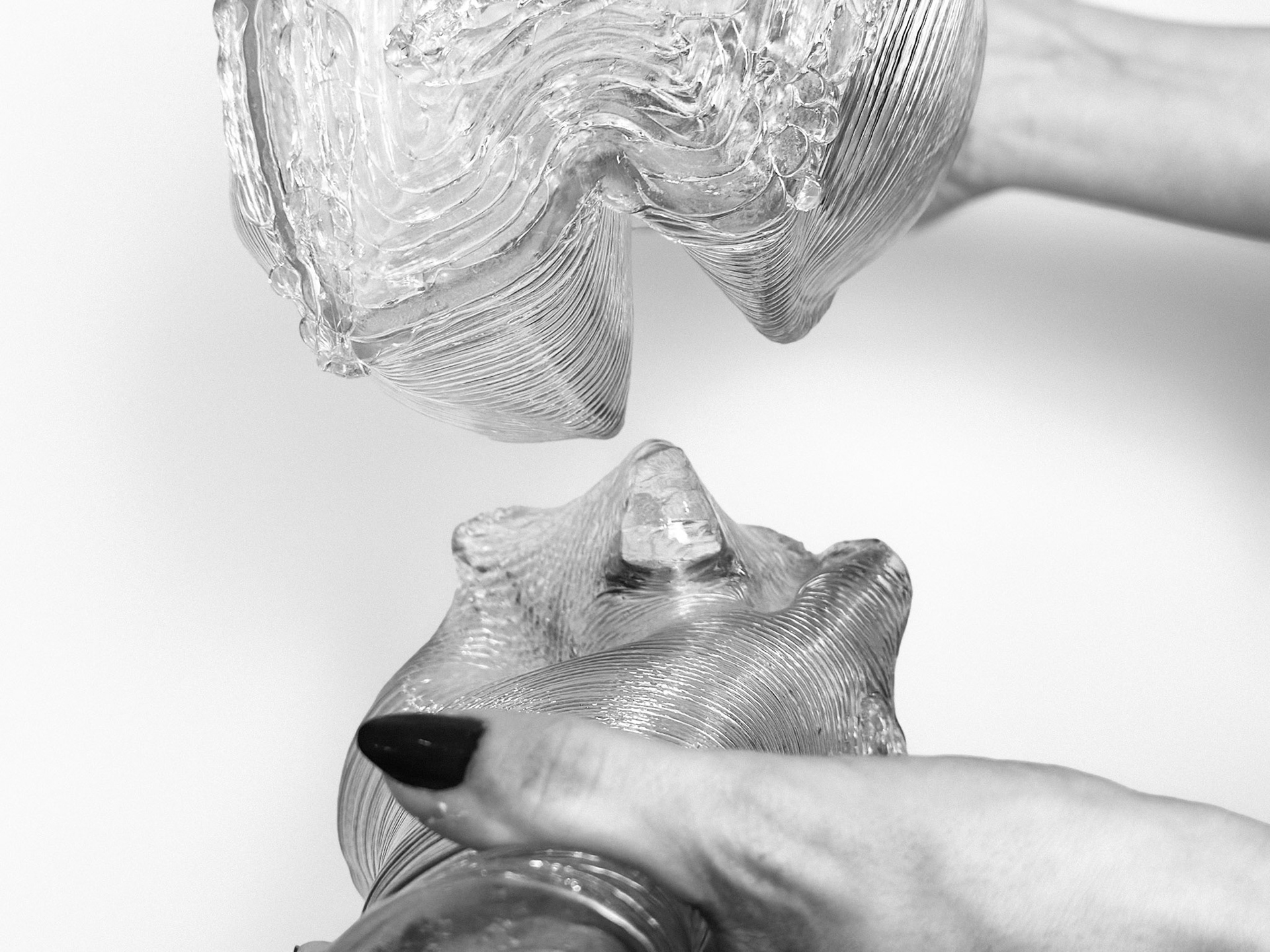
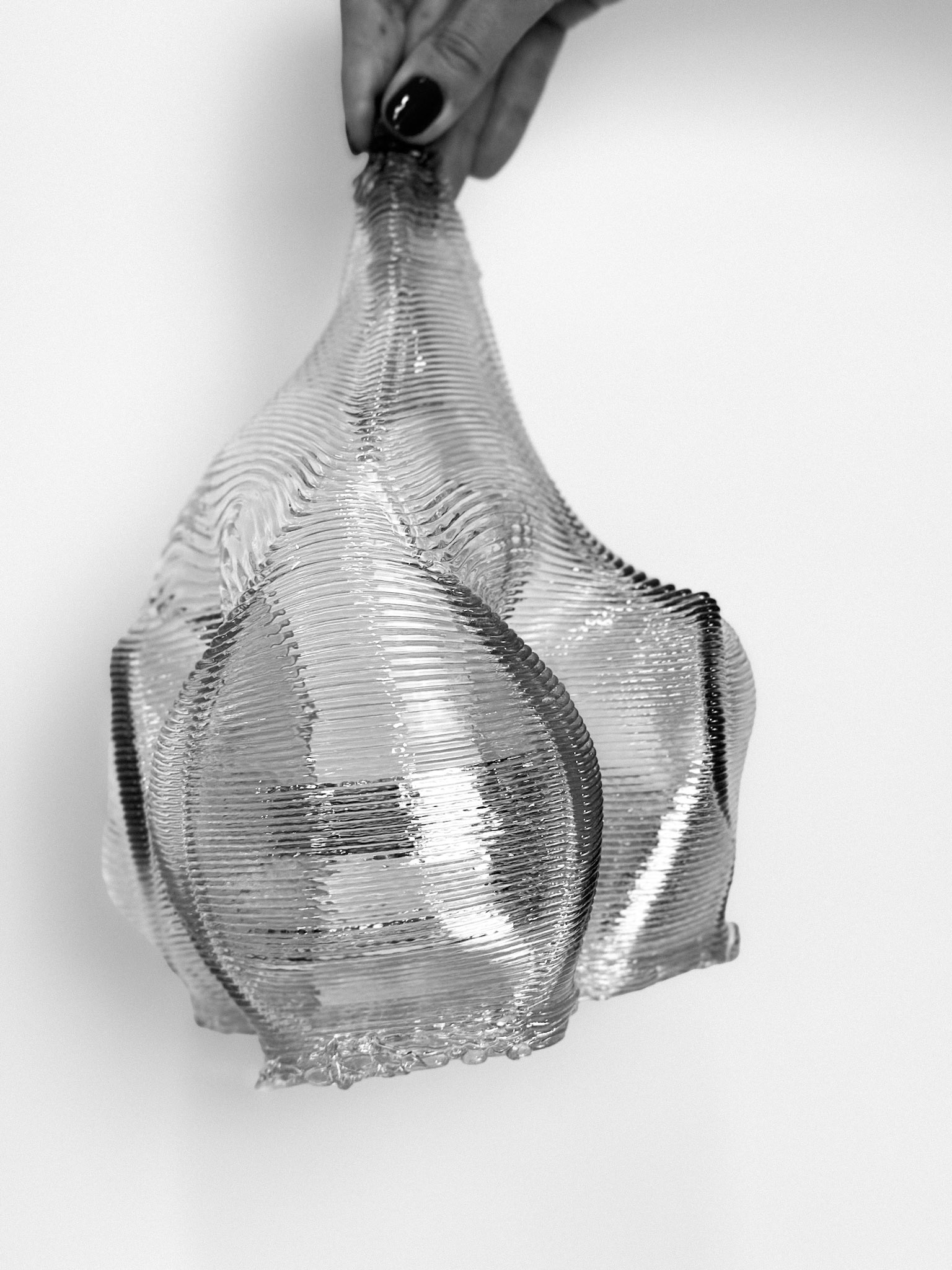
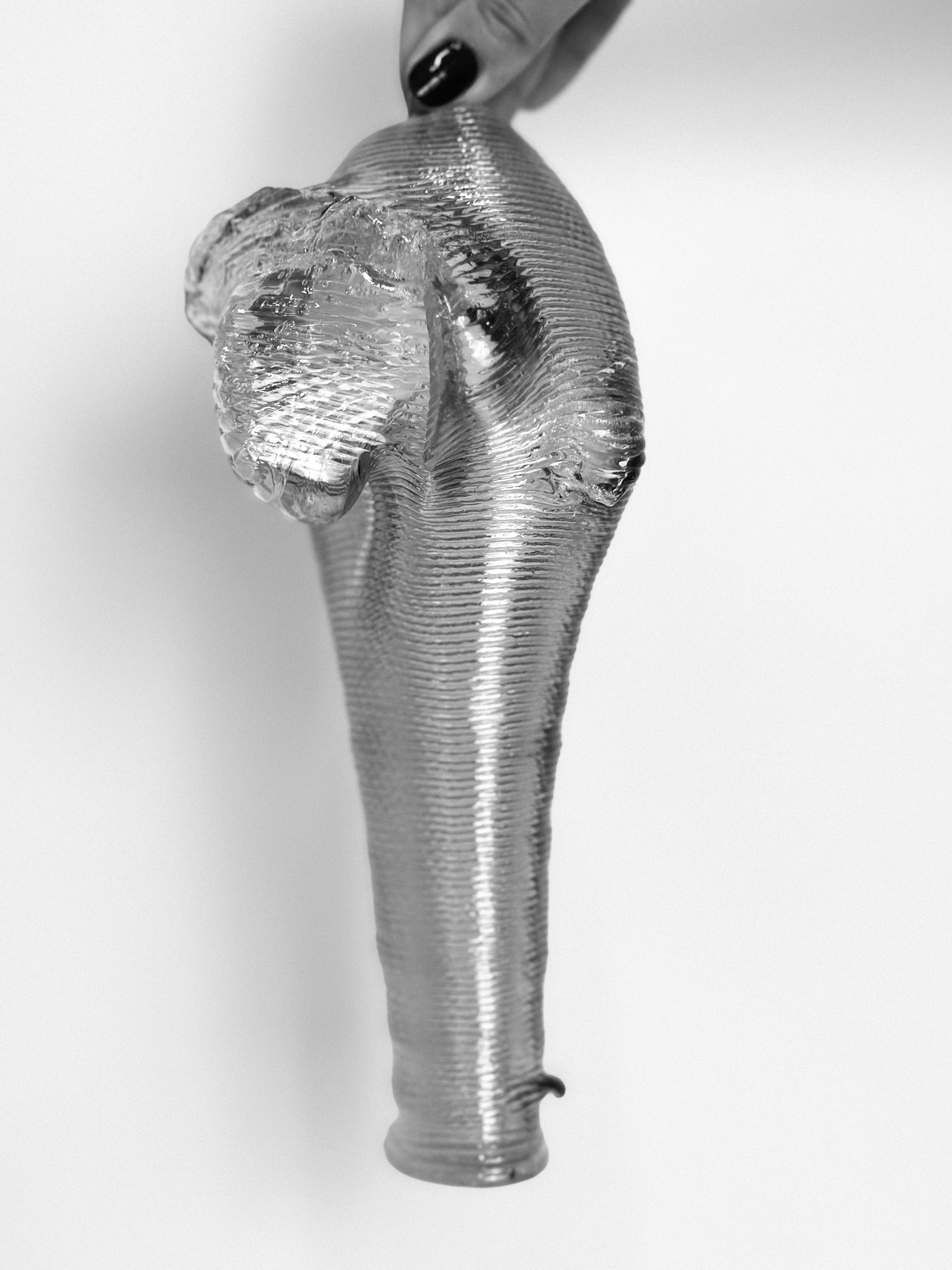
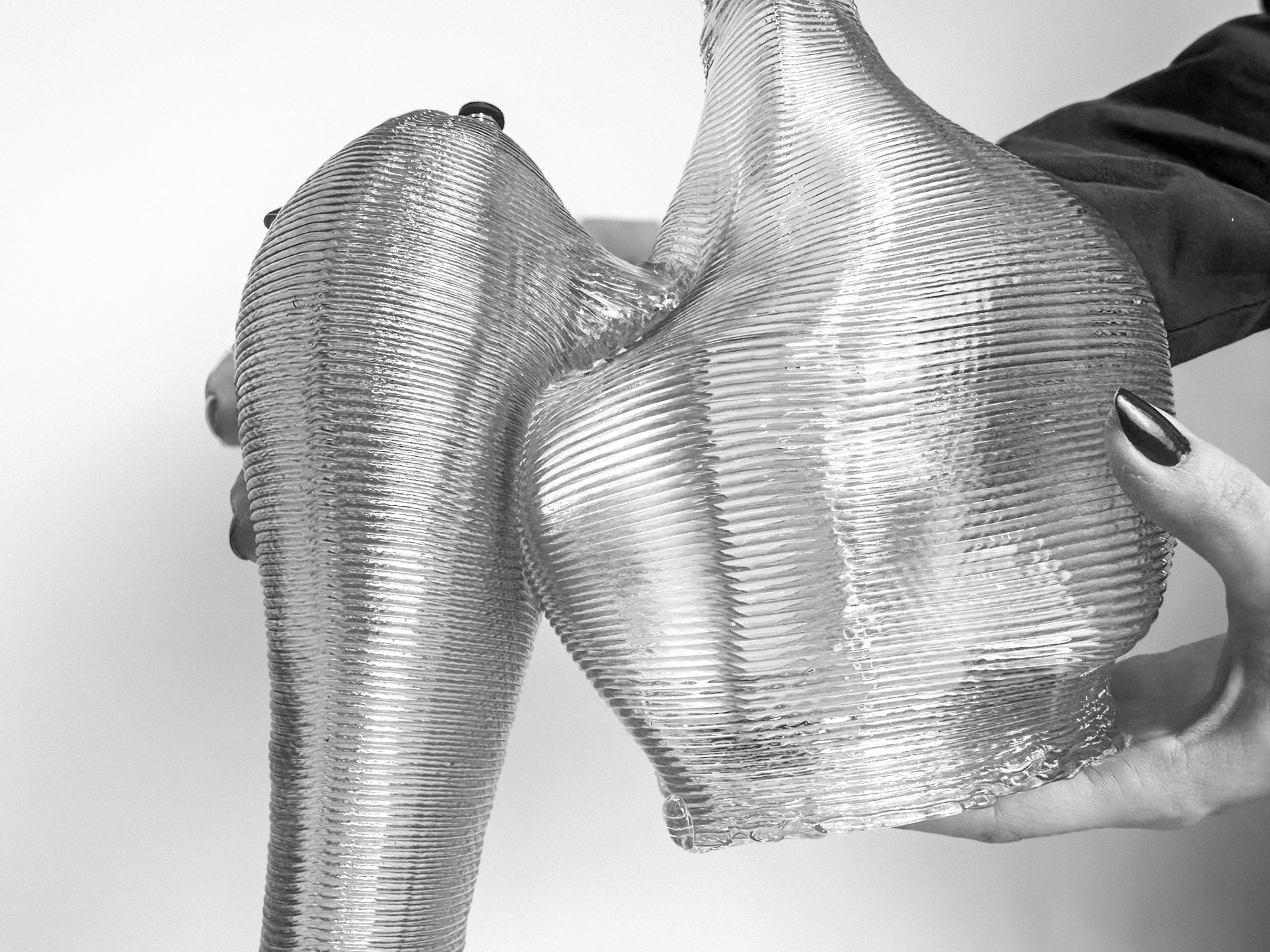
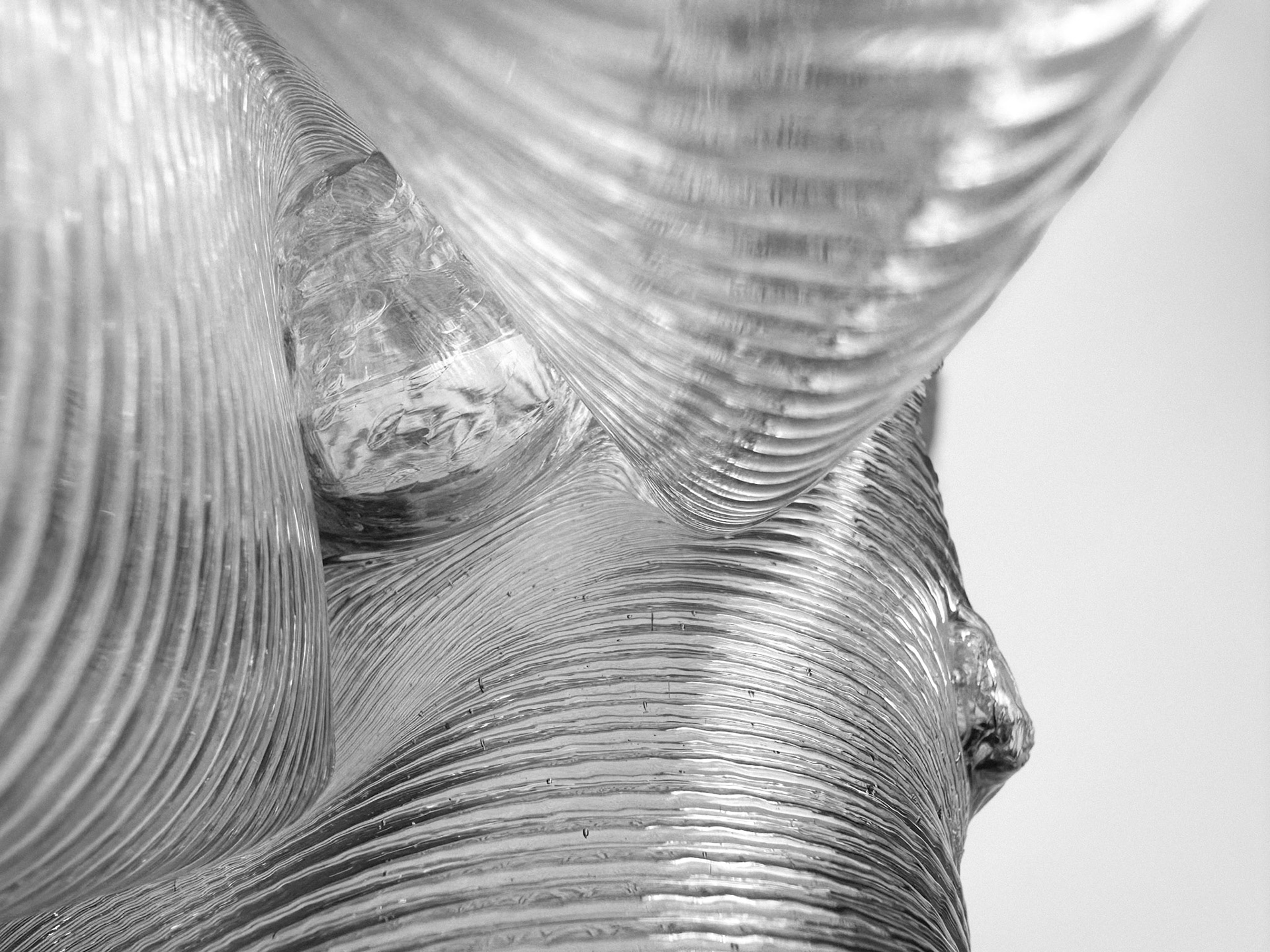
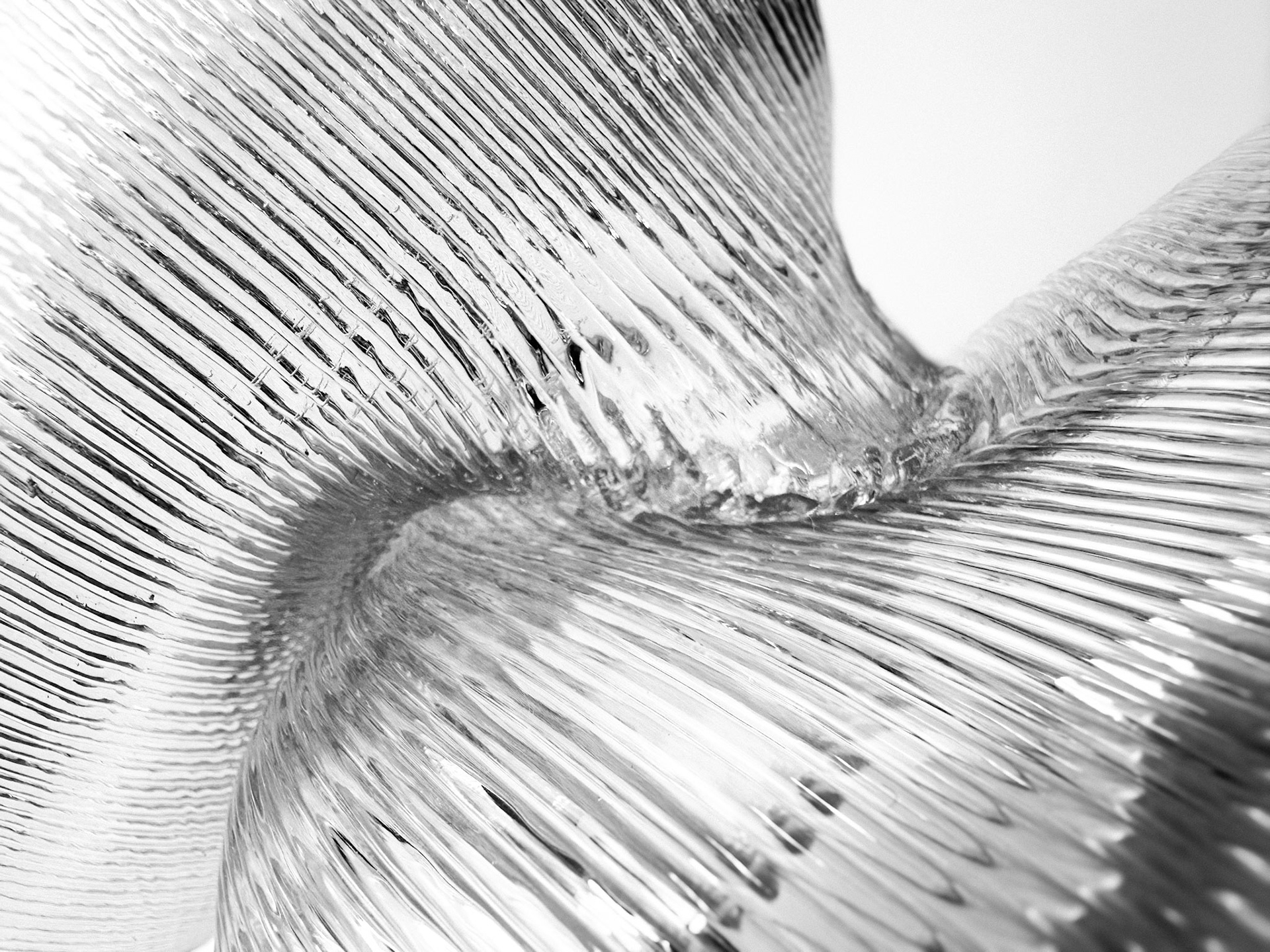